EE Bench
Jörg Vollrath, University of Applied Science Kempten, Germany, Joerg.vollrath@hs-kempten.de
Newer document version: Research summary
Abstract
Electrical engineering needs a laboratory containing power supplies (logic, analog positive and negative, reference),
arbitrary waveform generators, digital inputs and outputs, voltage and current measurements and an oscilloscope (4 channels).
This equipment should be usable as
semiconductor parameter analyzer (high accuracy measurement with curent and voltage limits),
spectrum analyzer (high resolution ADC), digitzer (many channels with many samples),
data logger (SD-card, battery supply) and sensor actuator interfaces (I2C, SPI, PMOD, Bluetooth).
Measurement of electrical systems with IV curves, signal time behaviour and transfer functions (bode diagram) is one application.
High accuracy, high speed and low noise measurements are required for data converters and need special measurement procedures.
For prototypes serial transmission and receiving circuits, digital signal processing facilities
and control blocks enable system development.
A nice web user interface and no software installation would enhance the usability.
This paper tries to develop such systems.
|
|
First the current status of the project showing the hardware, the VHDL files,
the nodejs files and the user interface is shown.
Then the proposed system overview is given.
For the FPGA hardware the data acquisition, triangle, sine signal generator,
UART and data buffer circuit description in VHDL is presented.
This specifies also the serial communication over the USB connector
used by the nodejs server.
Next the user interface for AWG, oscilloscope, FFT and histogram was developed
and is shown here for the hardware.
Finally a data converter characterization is done.
14.11.2023 How to Install Version V06
Version V06 Installation
Status 30.01.2023 Version V06
The Figure shows the BASYS3 FPGA board (150.- Euro) with 4 XADC channels
at the left side and a 16 Bit 100k Ohm R2R DAC connectd to 2 PMODS on
the right side. Next the configuration files for the FPGA and Node.js
project can be downloaded. After installing Nodejs on a Windows PC this
enables the web interface presented in the next figure to control
an arbotrary waveform generator (AWG), an oscilloscope, a FFT and
a histogram. A complete open electronics laboratory is therefore available.
This documents tries to describe the open system and enable system
extensions and modifications.
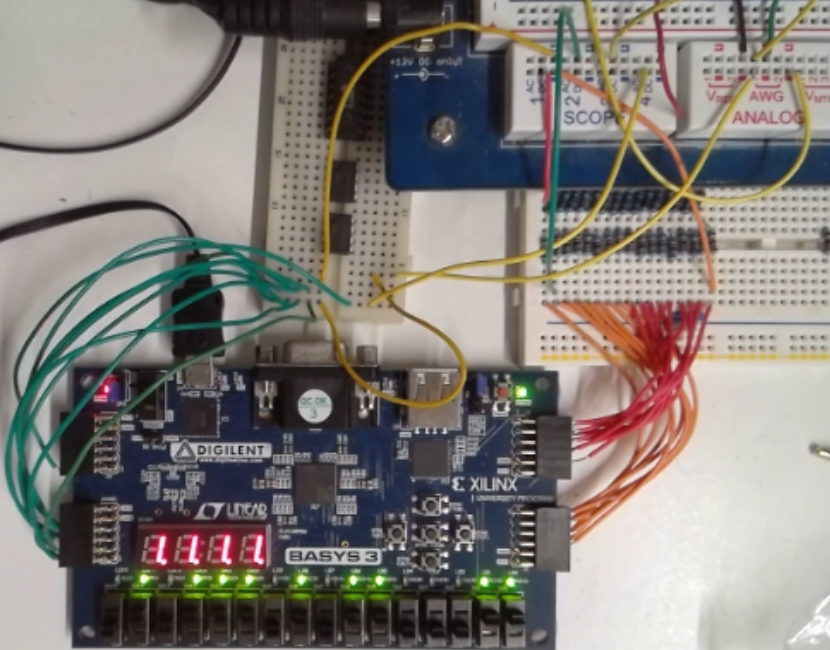
Figure: BASYS3 FPGA Board with R2R DAC and Electronic Explorer
VHDL project files EEBench_V06
Node.js project files NodeEEBench.bat as zip V06
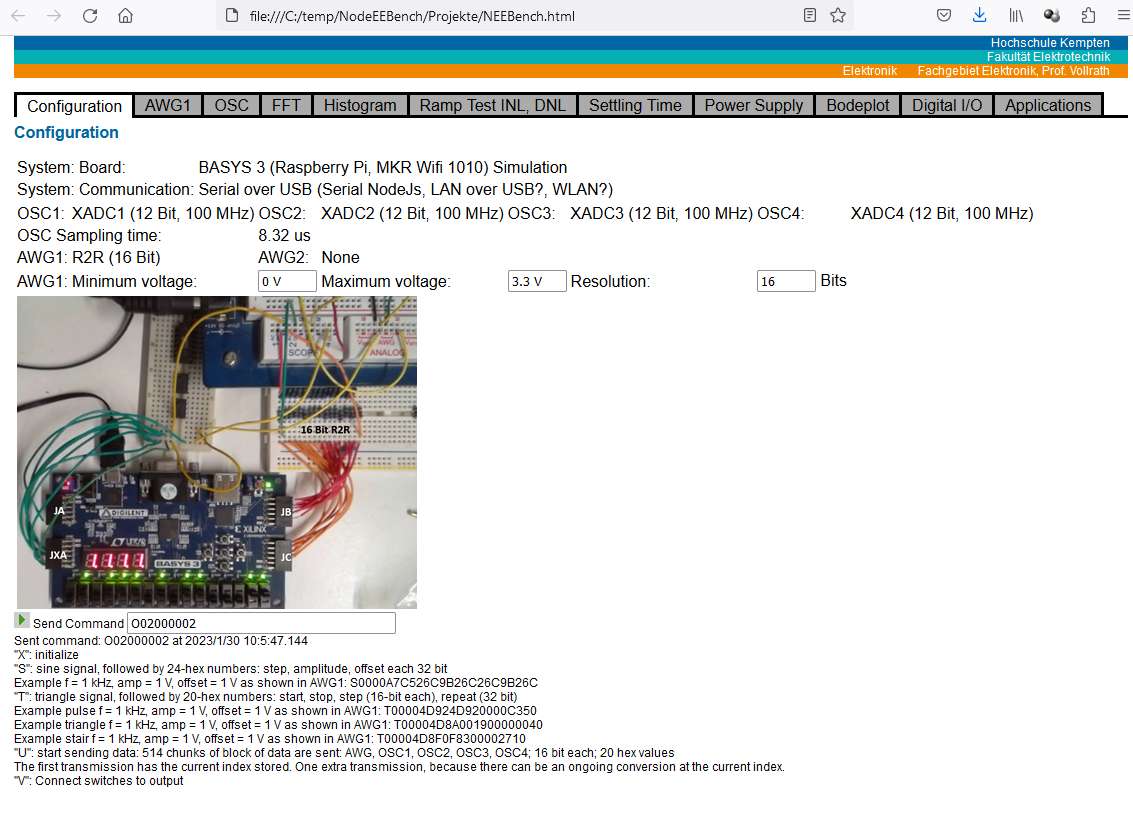
Figure: Nodejs, NEEBench user interface configuration page
Proposed system overview
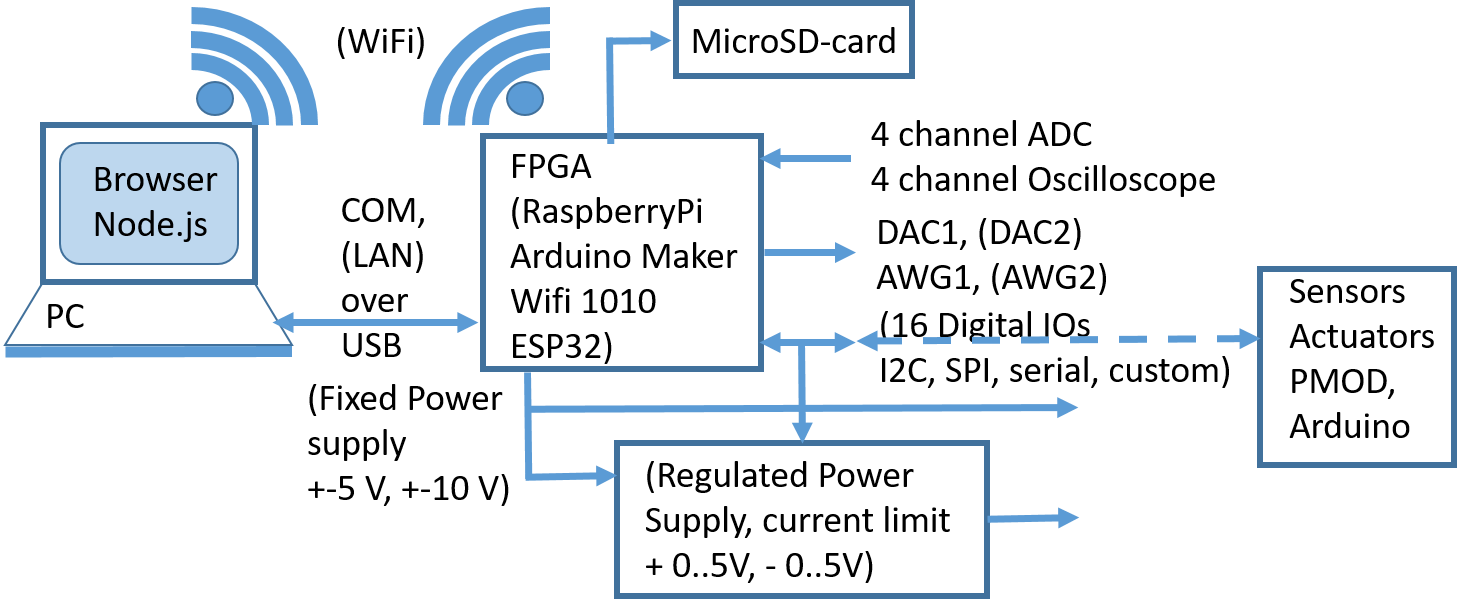
Figure: Propsed system overview
The figure shows the overview of the ideal proposed system. Functions in brackets are not implemented yet.
Features of BASYS 3 System and Software
- System: BASYS 3 with 230400 Baud serial interface over USB
- AWG: 1 channel, 16 Bit R2R, 0..3.3V output range, 7.7 MHz sine
- OSC: 4 channel, XADC 1MSps (multiplexed x8) to 125 kHz, 0..1 V input range, up to 4k points
- The original digital code of AWG1 can be displayed as reference
- Variable buffer size is implemented
- FFT: up to 4k points signal and noise calculation, histogram display
- DAC characterization interface
- Switching between code display, voltage display
- Special trigger for ramp up test
Next steps
- 16 Bit R2R DAC characterization
- Power supply for positive and negative voltages
for operational amplifiers to buffer the DAC AWG output.
- DAC characterization interface
- ADC upgrade: 24-Bit ADC, I2C, 16kSs, 6 channel MAX11259 PMOD 90.- expensive
- 2nd channel AWG: 16-Bit DAC, 1 channel, 100 kHz, SPI, MAX5216 23.-;
MCP4728 12-Bit DAC, 4 channel, 6us ca. 125 kHz, Command 3.4 MSps 15.-
- AWG: White noise vector memory
- Bode plot
- Pipeline ADC with characterization interface
- Arduino Maker WiFi 1010
- PMOD DA2 ( 2 channel, 12-Bit, 125 kHz, 8 µs) 20.-
- PMOD AD2 ( AD7991 4, channel, I2C, 1 us conversion time, 12-bit ) 20.-
- Serial DAC
- ESP32
- RaspberryPi
- Simulator
- ZYNQ FPGA
- Test sequence control and interface
Use cases for this system
Applications can be an audio amplifier with microphone and speaker, filters,
buck and boost converters, charge pumps, data converters,
and motor control
An AWG1 generated signal (analog, digital IO) is measured with OSC1 and fed to an analog LCR filter circuit,
or a SC-filter circuit (Digital switch control signals), or digital to a microprocessor and measured
with OSC2 or (calculated digital signal).
The internal signal from OSC1 can be digitally processed internally and
fed to AWG2 (analog and digital IO) and measured with OSC4 to compared it with the other solutions.
Static IV curve (Transistor, Diode, Opamp)
Bipolar transistor: UBE, IB (2 OSC channels), UCE, IC (2 OSC channels)
High current source with current limit IC
Low number of measurement points
Sine signal circuit analysis (amplifier, filter)
Positiv and negativ power supply (OpAmp), sine signal generator (AWG1),
4 channel signal measurement
Bode plot (Opamp, filter, LC meter)
Software control: AWG1, amplitude, frequency range, phase measurement
White noise generation and FFT
Signal processing
Digital FPGA logic or MACC blocks
Data converter characterization (offset, gain, INL, DNL, SNR, ENOB)
I. State of the art
Before this system was built available systems were reviewed:
- Electronic Explorer (Digilent/National Instruments) (665 Euro, 2022, 350 Euro, 2010)
- ADALM2000 (Analog Devices) (300 Euro, 2022)
- Red Pitaya (250..450 Euro, 2022)
- Analog Discovery (450 Euro, 2022)
- PicoScope 2000 (100..1000 Euro, 2022)
- SmartScope (270 Euro, 2022)
The Electronic Explorer was the cheapest (350.- Euro, 2010) and most
versatile (4 channnel oscilloscope and breadboard) system having now
only 2 oscilloscope channels and a price hike to 650.- Euro (2022).
The Electronic Explorer has a very nice user interface,
which is of no cost and can be run in a demo mode without hardware.
The ADALM2000 is very cheap and has most of the functionality. It provdies a web server
over USB connection, but needs a phyton install for software.
The Red Pitaya has a web interface and needs no software to be installed.
Unfortunately also here a price-hike for higher precision was happened.
Most of the systems provide also a very detailed hardware description (schematic).
Example:
Analog Discovery circuit description
A data converter code (not voltage) based control should be available.
The digital data of the AWG should be easily available.
There seems to be a trend to have only 2 oscilloscope channels
and to increase the selling price for these systems.
Detailed tutorials to modify hardware and software are limited.
There seems to be room for a very cheap electronics laboratory.
This can be compared to the situation in the microprocessor realm
where a very low cost Raspberry Pi Zero after the first generations of
Raspberry pi is a huge success.
Basic and optimum system specification
Basic:
- 4 channel oscilloscope
- 2 arbitrary waveform generators
- Positive, negative, logic (3.3/2.5V) power supply
- 16 Digital IOs
- Breadboard with interface
Optimum:
- Web based user interface and simulation mode
- Digital IOs with digital interface (I2C, serial, SPI, gray code)
- Bode diagram
- IV curves: diode, transistor, opamp
- Data converter characterization with calibration
- Digital signal processing: filters, control elements, switched capacitor circuits
System overview
Software installation and updating is always difficult. The best solution would be, if the system
is providing a WiFi or LAN connection via USB that can be operated via the browser.
The ADALM provides a LAN connection via USB, but there is no web interface available.
Most systems provide only a serial interface over USB. Therefore a nodejs application is built,
which can be installed to provide a web interface and talks via the serial interface to the system.
A simulation mode should enable running the system without hardware.
Hardware solutions
A suitable low cost hardware was chosen for this project.
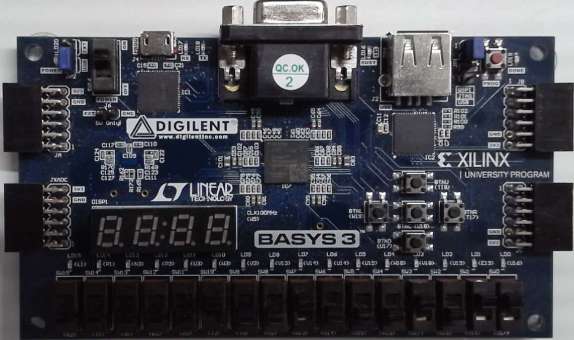 BASYS3 |
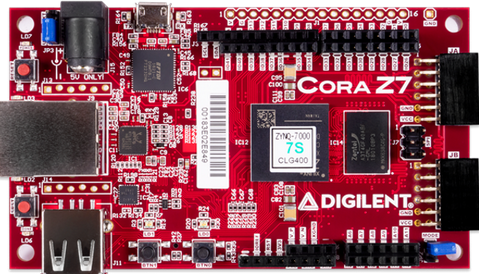 CORA Z7 |
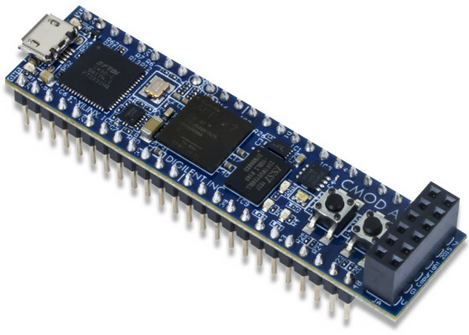 CMOD A7 |
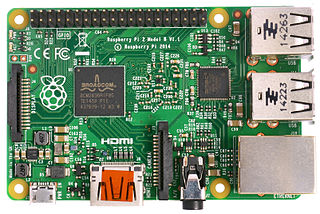 Raspberry Pi |
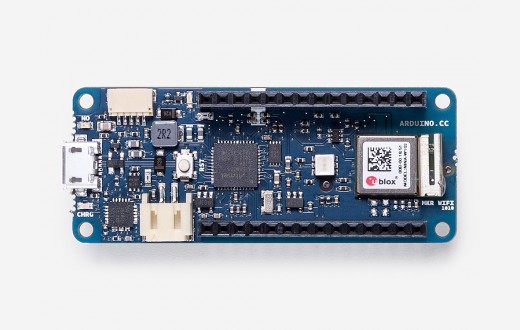 MKR Wifi 1010 |
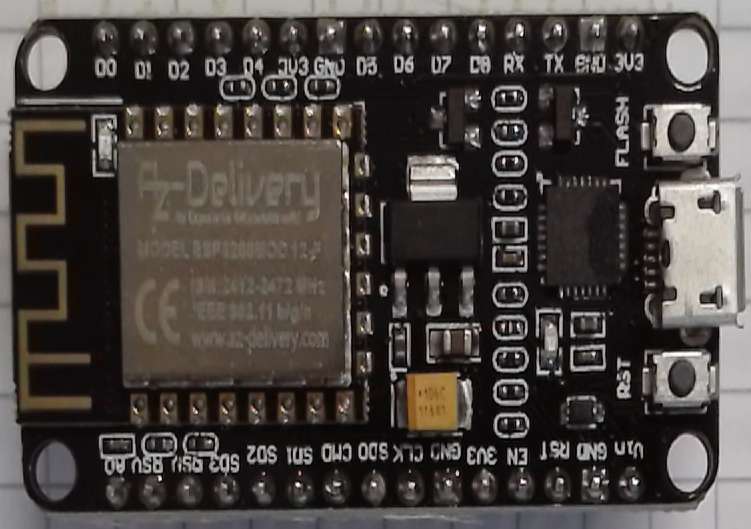 ESP32 |
Figure: BASYS3, CORA Z7, CMOD A7, RaspberryPi, MKR Wifi 1010 and ESP32
The BASYS 3 board is used for the laboratory digital electronics.
In this review ALTERA FPGA boards are still more expensive then Xilinix FPGA boards.
The MKR Wifi 1010 is used for laboratory Interface electronics.
Raspberry Pis and ESP32 boards are used for various student projects.
Target:
- BASYS3 FPGA (140 Euro) (CMOD A7 (SRAM) 120.- Euro)
- CORA Z7 FPGA, uP(150 Euro)
- RaspberryPi (10.- - 100.- Euro)
- MKR Wifi 1010 (35.- Euro)
- ESP 32 (12.- Euro)
For 'Interface Electronics' a NEXYS3 and MKR Wifi 1010 board were used
for the laboratory. The usage was very limited and data was only send to
the serial interface with no user interface.
- NEXYS 3
- MKR Wifi 1010
- 8 Bit, 300 Sps, R2R DAC
- 2 chan, 12-Bit, (125kHz) PMOD DA2 (20.-)
- 4 chan, 12-Bit, 1 MSps PMOD AD2 (20.-)
The available BASYS3 board was chosen as starting point.
In the next section the developed VHDL code is presented.
FPGA Realization
Since VHDL code is more difficult than JavaScript client code as much calculation and verification
as possible is put on the client side.
First the ADC implementation with the XADC is presented and then the arbitrary
waveform generator for pulse, triangle, dc and sine signal.
Then the UART interface for control and data transfer is realized
and commands are specified.
Extensive simulations of the circuits were done.
Finally a data buffer with control was realized.
XADC Wizard
The XADC can sample 4 differential channels on the BASYS3 board multiplexed.
Input range is 0..1V.
Sampling is done at 1 MSps multiplexing 4 channels.
Lower row JXADC is negative input, upper row positive input.
The FPGA has more XADC pins which can be used, but these are not carfully routed.
https://www.youtube.com/watch?v=2j4UHLYqBDI
- Basic:
- Interface Option: DRP
- Timing mode: Continous mode (always running)
- Startup Channel selection: Channel sequence
- DRP Timing options: 100MHz (Board frequency), 1000kS/s (maximum speed)
- ADC Setup
- Continous, Averaging None
- Alarms: unchecking not used
- Channel sequencer: choose channels
vaux6,7,14,15
Lower folder IP Sources: Instatiation Template: VHDL vho
Basys 3 FPGA xc7a35tcpg236-1
A file XADC_EE.xci is generated with the XADC interface.
my_adc : XADC_EE
PORT MAP (
di_in => "0000000000000000", -- input wire [15 : 0] di_in
daddr_in => daddr_in, -- input wire [6 : 0] daddr_in hex 16,17,1e,1f
den_in => enable, -- input wire den_in
dwe_in => '0', -- input wire dwe_in
drdy_out => ready, -- output wire drdy_out
do_out => data, -- output wire [15 : 0] do_out
dclk_in => CLK, -- input wire dclk_in
reset_in => BTN(4), -- input wire reset_in
vp_in => vp_in, -- input wire vp_in
vn_in => vn_in, -- input wire vn_in
vauxp6 => JXA(0), -- input wire vauxp6
vauxn6 => JXA(4), -- input wire vauxn6
vauxp7 => JXA(2), -- input wire vauxp7
vauxn7 => JXA(6), -- input wire vauxn7
vauxp14 => JXA(1), -- input wire vauxp14
vauxn14 => JXA(5), -- input wire vauxn14
vauxp15 => JXA(3), -- input wire vauxp15
vauxn15 => JXA(7), -- input wire vauxn15
channel_out => channel_out, -- output wire [4 : 0] channel_out
eoc_out => enable, -- output wire eoc_out
alarm_out => alarm_out, -- output wire alarm_out
eos_out => eos_out, -- output wire eos_out
busy_out => busy_out -- output wire busy_out
);
The connector JXA is used for measurement and data gives a converted 16 bit value.
The channel is selected with daddr_in.
Triangle generation
A triangle should accomodate excercising all codes of a data converter.
Therefore start, stop and step values are needed.
For very low frequencies or large periods a repeat parameter is used.
It has to be verified that start is lower than stop, that step is positive greater than 0.
If the step size is not an integer times stop minus start the remainder has to be taken into account.
If step is bigger than stop minus start a rectangle waveform is produced.
Since VHDL code is more difficult than JavaScript client code as much calculation and verification is put on the client side.
The following relationship between FPGA frequency, signal frequency,
resolution (number of bits), start, stop and step should be valid.
Input: fsignal, fFPGA, NBit, start, stop
For rectangle: step
output: (step), repeat
tri_unit: tri_counter
port map(
clk => CLK,
reset => xrst,
start => tstart, -- in std_logic_vector(15 downto 0);
stop => tstop, -- in std_logic_vector(15 downto 0);
step => tstep , -- in std_logic_vector(15 downto 0);
repeat=> trepeat,-- in std_logic_vector(31 downto 0);
q => tout
);
1. Calculation Rectangle:
The following variables are used for calculation.
Maximum Code of DAC: maxC, maximum voltage of DAC: maxV, AWG offset value: off,
AWG amplitude value: amp
var maxV = 3.3;
var maxC = 32767;
start = Math.trunc(maxC / maxV * (off-amp)); // start voltage to code
stop = Math.trunc(maxC / maxV * (off+amp)); // stop voltage to code
if (start < 0) start = 0; // no negative code
if (stop > maxC) stop = maxC; // stop limited by maximum code
step = stop - start; // adjust step to difference
repeat = Math.trunc(1 / frequency / 2 * 1E8); // 1E8 fFPGA
The 16-bit R2R 100k, 220k DAC needs 15 us settling time.
The amplitude decreases above 30 kHz.
2. Calculation Triangle:
The code is the same for start and stop.
The difference is in the calculation of repeat and step.
repeat = 1 / frequency / (stop-start) / 2 / 10E-9; // 1E8 fFPGA
if (repeat >= 16) {
repeat = Math.trunc(repeat);
step = 1;
} else {
step = Math.trunc(16 / repeat);
stop = Math.trunc((stop-start)/step)*step + start;
repeat = 16;
}
Due to the rounding the actual frequency is only
closely matching the required frequency.
Table: Amplitude 3 V.
Required frequency | 5 Hz | 50 Hz | 100 Hz |
200 Hz | 300 Hz | 500 Hz | 1 kHz | 10 kHz |
Actual frequency | 5.22 Hz | 50.86 Hz | 98.7 Hz |
98.7 Hz | 197 Hz | 394 Hz | 888 Hz | 9.39 Hz |
There seems to be some more work needed.
3. Calculation Stair
A fixed number of 5 steps up and 5 steps down is implemented.
repeat = Math.trunc(1 / frequency / 2 / 10E-9 / 5); // 1E8 fFPGA
step = Math.trunc((stop-start)/5);
stop = Math.trunc((stop-start)/step)*step + start;
For a set of IV curves one generator can be programmed with a staircase
and the other with a synchronized higher triangle frequency.
With the prepared list 1 kHz and 5 kHz or 2 kHz and 10 kHz can be used.
Sine generation
Research for realization of a sine generator in FPGA gives most of the time LUT solutions.
Values for sine are stored in a table and looked up. This is only feasable for small resolutions (up to 8 Bit).
LUTsize = NBit * 2
NBit
Table: Resolution and LUT table size
Resolution (Bits) | 8 | 12 | 16 | 20 | 24 | 28 | 32 |
Lookup table size (Bits) | 2k | 48k | 1M | 20M | 402M | 7.5G | 137G |
Calculation of sine can be iteratively done using complex calculations.
This can be used for iterative calculation with accumulated error or
bitwise calculation for a certain value.
Iterative calculation minimizes computation effort between steps,
bitwise calculation increases computation effort for each bit.
A combination of a limited LUT table 32..256 values or 5..8 bits
and sine calculation would be an optimum solution.
Next value Re = (Current value Re * Step size Re - Current value Im * Step size Im)/2N
Next value Im = (Current value Re * Step size Im + Current value Im * Step size Re)/2N
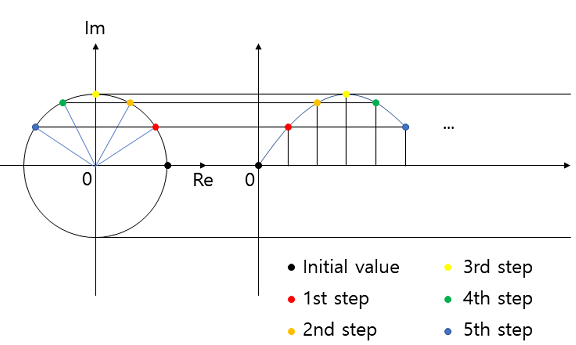
Figure 1: Example of complex number multiplication.
Challenges are:
- Signed large number multiplication in one clock cycle
- Rounding and Accuracy
- Transfer to a positive number (amplitude, offset)
- Calculating step size (Φ and complex numbers)
This can be used to iterative generate the next step or using all bits
to generate a sine for an absolute value.
32 Bits would require 32 steps to get to the final value.
During these 32 steps sine is iteratively computed.
Verification of this procedure is done using FFT and looking at signal to noise ratio.
Since Xilinx DDS Sine Wizard gives up to 24 Bits resolution this
realization targets 32 Bit.
- Precalculation of 32 to sine and cosine values for power of 2 fractions
sine(2 · π / 232 · 2i )
i=0..31
- Precalculation for a given frequency of step sine (Im) cosine (Re) by
using for each bit the precalculated values
- Generating sine values
Applying the step to the current value
Accurate calculation for the next value 32*steps
Input and outputs for sineX VHDL module are:
sine_unit: sineX -- Sine generator
Port map (
CLK => CLK,
RST => xrst,
step => step, -- increment in (31 downto 0) 32 bits
amplitude=> amplitude, -- signal amplitude in (31 downto 0) 32 bits
offset => offset, -- signal offset in (31 downto 0) 32 bits
mysine => mysine -- output waveform out (31 downto 0) 32 bits
);
Sine Calculation example
fFPGA = 100 MHz
fsignal = 10 kHz
Number of points per cycle: Np = fFPGA/fsignal = 10000
step = 232 / Np = 429497
An FFT needs a power of 2 samples without windowing and an
odd number of cycles to excercise as many levels of a data
converter as possible
Choose NFFT:
NFFT (NBit) = 256 (8), 1024 (10), 16k (14), 1M (20), 16M (24), 1G (30)
Choose number of cycles:
Ncycle = 1, 11, 101, 1001, 100001
Calculate signal frequency:
Tsignal = NFFT / fFPGA / NCycle
fsignal = 1 / Tsignal = fFPGA * NCycle / NFFT
step = 232 / fFPGA * fsignal =
232 / fFPGA * fFPGA * Ncyle / NFFT =
232 * Ncyle / NFFT
NFFT = 1024
Ncycle = 17
fsignal = 100 MHz * 17 /1024 = 1.66 MHz
step = 71303168 = 04400000
Number of cycles | frequency in kHz | Step |
3 | 1.40851 | 196608 = 3 * 64 * 1024 |
11 | 5.16452 | 720896 = 11 * 64 * 1024 |
101 | 47.419625 | 6619136 = 101 * 64 * 1024 |
+ Sine Simulation with JavaScript to verify VHDL
- Sine Simulation with JavaScript to verify VHDL
For VHDL verification Hexvalues were calculated using JavaScript to compare results.
Signed negative numbers and hex values
Javascript hex function works only with positive numbers.
Here the range is 32 bit which is equal to 2
32 = 4 *1024* 2014 *1024.
signed to unsigned exampe std_logic(11011001) = signed -39 = unsigned 217.
Add +256 to the negative number and then convert to hex.
Digitaltechnik
Sine generation
A test bench for logging the VHDL created values was written: tb_TOPLOG.vhdl in the project SineX
using TOP.vhd and txt_util.vhd.
The values are written with txt_util.vhd to a file "mysine0_everysteps_out.txt" in the directory
C:\temp\DT\Sine_Gen\Sine_Gen.sim\sim_1\behav\xsim
Data was inserted into
JavaScript FFT.
Depending on the number of FFT points and the number of cycles the following SNR can be reached.
NFFT | 256 | 1024 | 1024 | 16k | 64k |
cycles | 17 | 17 | 17 | 17 | 17 |
amp | 400 | 400 | 7FF | 7FF | 7FF |
SNR | 156.46 | 156.73 | 156.72 | 163.28 | 156.45 |
Oscilloscope
5 channel acquisition data are continously written into block memory.
The current position and the number of samples is stored in position 2 and 3.
These data are serially transmitted to the NodeJS server and then to the client (OSC).
The client sorts the data according to the bCount position (OSC1).
The trigger condition is searched in this data and data before and after the trigger point are
extracted and displayed (OSC2).
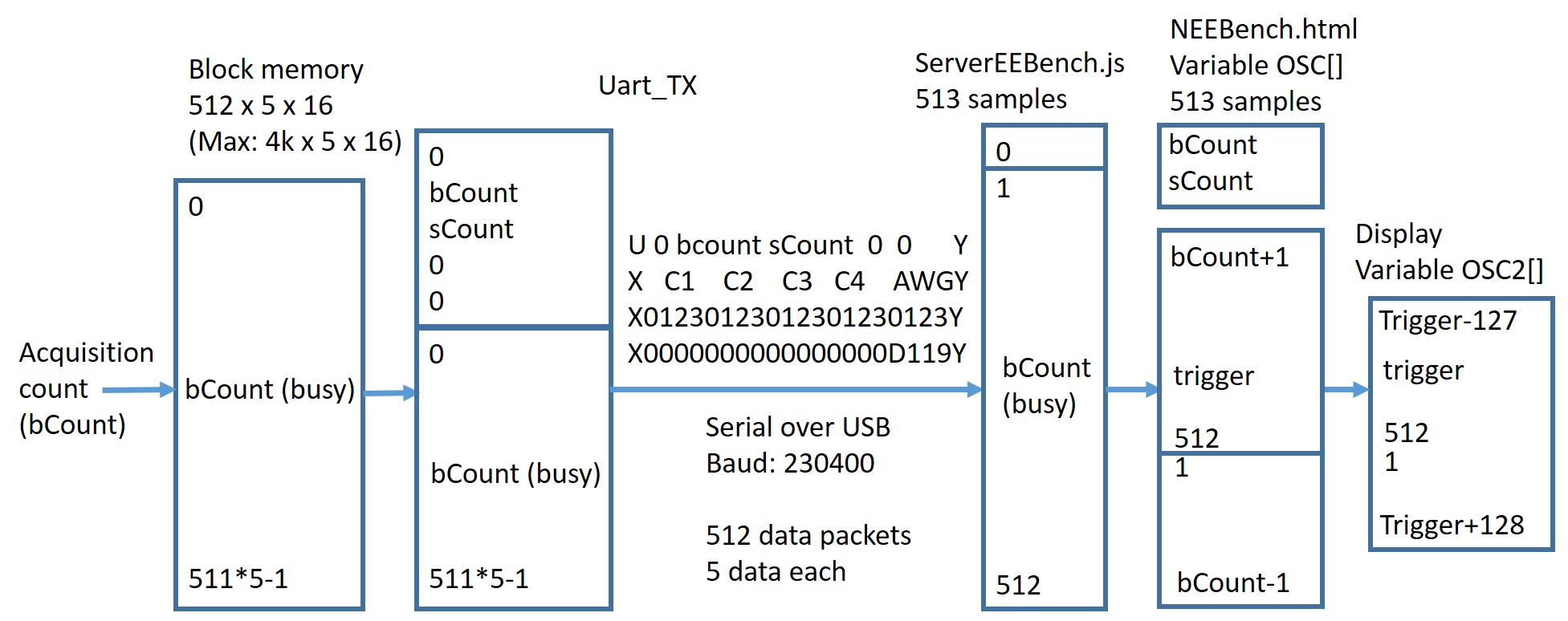
Figure: Acquisition
Details can be found in "Data Acquisition"
UART
Since the received data is directly stored in signal generator registers there is no need for a FIFO.
Implemented commands (uart_mem.vhd, getCmd: process):
"X": initialize
"S": sine signal, followed by 24-hex numbers: step, amplitude, offset each 32 bit
"T": triangle signal, followed by 20-hex numbers: start, stop, step (16-bit each), repeat (32 bit)
"U": start sending data: 514 chunks of block of data are sent: AWG, OSC1, OSC2, OSC3, OSC4; 16 bit each; 20 hex values
The first transmission has the current index stored. One extra transmission,
because there can be an ongoing conversion at the current index.
"V": Connect switches to output
"O": Oscilloscope block size 16 bit and sampling rate 16 Bit (V_06)
Command: O00200000 : Block size x0020 = 512; timeBase 0000 8.32 us
The mapping of uart_mem to block memory not registers is done starting EEBench_V04.
The multiplexer for sine, triangle switch is also done in EEBench using signal waveselect.
Baud rate 19200, 52us per bit, sine command: 25(chars)*10(Bit)*52us(bit time) = 12.5 ms
Baud rate 230400, 4.34 us per bit, sine command: 25(chars)*10(Bit)*4.3 us(bit time) = 1.1 ms
Baud rate 230400, 512 points 22 hex values each T = 0.5 s
+ EEBench V02
- EEBench V02
Used Modules (XADC omitted):
EEBench.vhd,
Test bench: tb_EEBench.vhd,
SevenSegDH.vhd,
Debouncer: debouncer.vhd,
Button Debouncer: ButtonD.vhd,
Clock divider for sine enable: CLK_DIV.vhd,
Sine generator: MACC.vhd,
complex vectors for sine: phi_export.vhd,
Pipeline multiplier for sine: pipe_mul.vhd,
Triangle generator: tri_counter.vhd,
Baud rate generator: mod_m_counter.vhd (Chu),
(UART FIFO: fifo.vhd not used anymore),
(UART: uart.vhd not used anymore),
UART to register: uart_mem.vhd,
UART receiver: uart_rx.vhd,
UART transmitter: uart_tx.vhd,
Pinout: Basys3_Master.xdc
The main module is EEBench having an UART, an oscilloscope (XADC channels) and
an AWG (arbitrary wave generator).
The UART of the FPGA receieves commands and transfers this information to registers.
The top module is uart_mem. Input is CLK (100MHz), rx reset and tx_mem memory for off FPGA
transfer and rx_mem as registers to receive commands from outside.
It uses the module uart_tx (transmitter), uart_rx (receiver) and
mod_m_counter (dividing the clock) for baud rate.
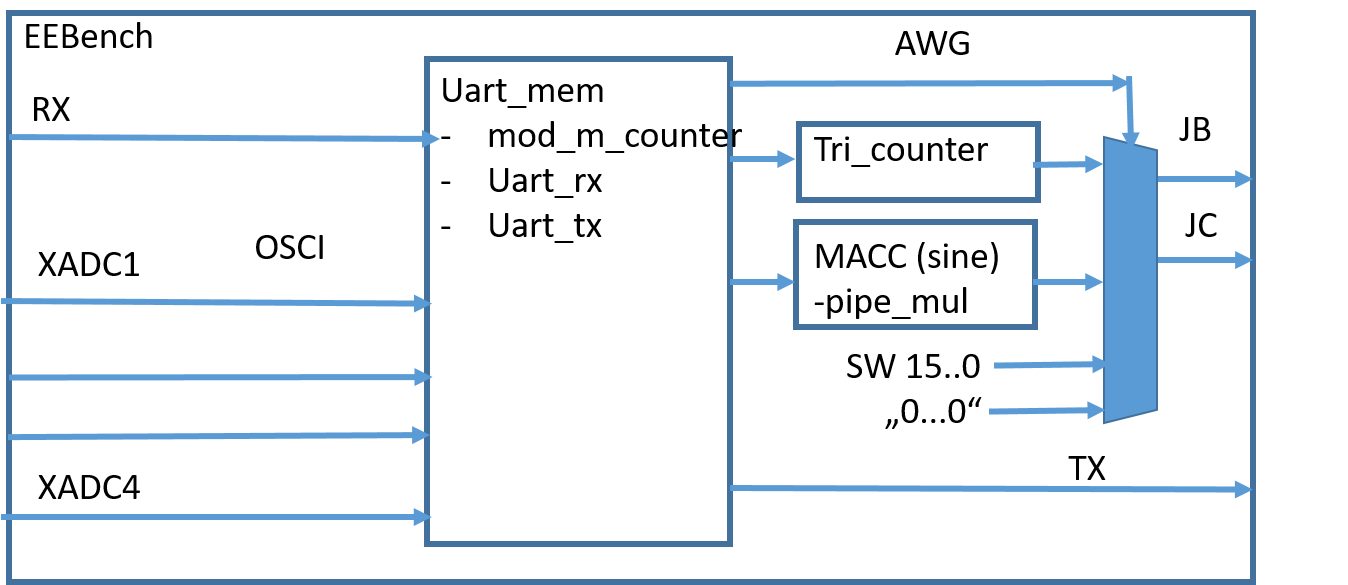
Figure: FPGA blocks for EEBench
A test bench tb_EEBench.vhd receives via the RX line with 19200 Baud the following commands:
V: show SW at the output
U: start memory block transmission
Simulation of the first version
T0000FFFF00010000: Initiate triangle waveform with Start, stop, step, repeat (4 hex digits each)
S7DA87F73185F5B402BDC4E6F87BFCCD800400000: Initiate sine waveform with
Step_Re, Step_Im, Step_Re1, StepIm1, sample (8 hex digits each)
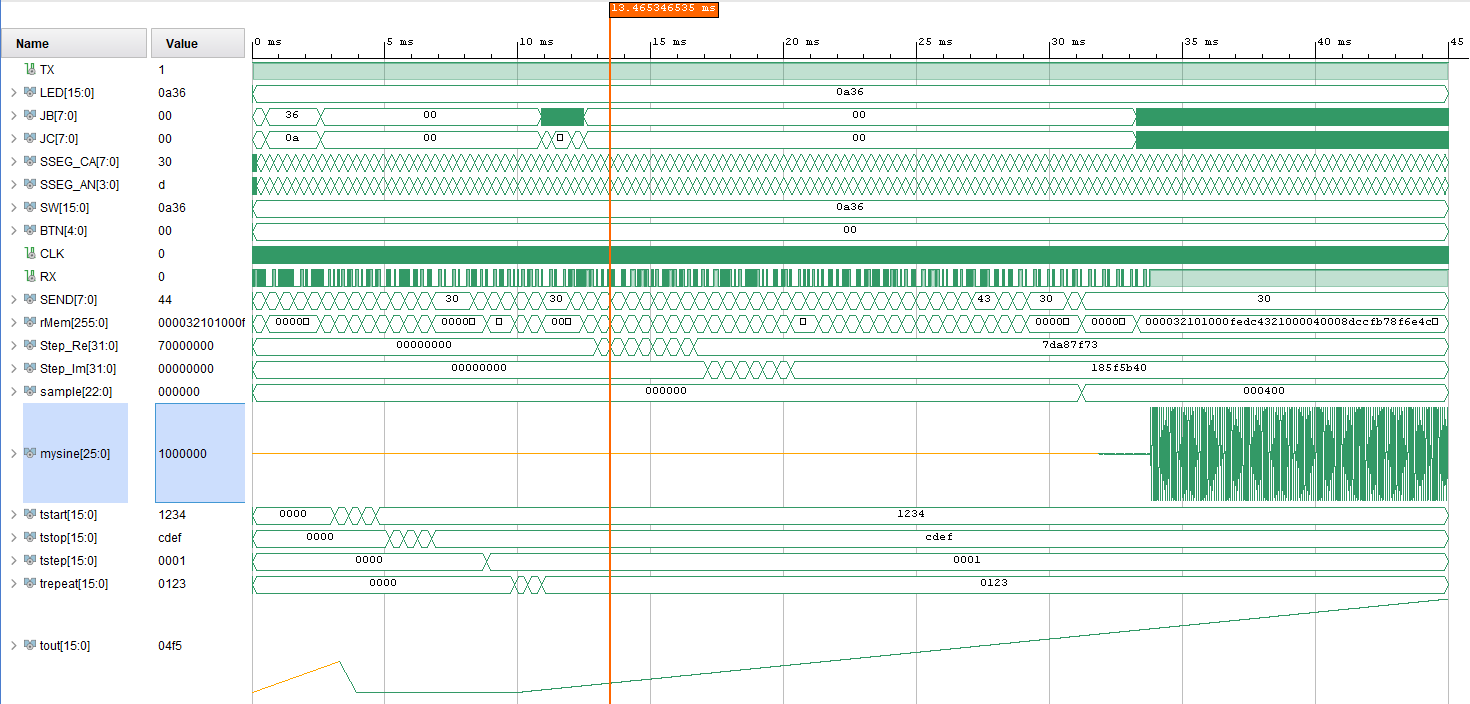
Figure: tb_EEBench.vhdl V01 simulation
The RX pin shows the received serial configuration data 50us each bit.
First the connection from the switches to JB (36) and JC (0a)
is activated (1..2 ms) via the V command.
The configuration data for the triangular waveform is
transmitted (tstart(5ms), tstop(7ms), tstep(9ms) and trepeat(11ms))
while the output JB, JC is set to "0000".
At 11 ms the triangle output (tout) is connected to JB, JC.
At 12.5 ms the configuration for the sine signal
starts (Step_Re set at 17ms, Step_Im 20ms, .. sample 31ms)
and the output JB,JC is set to "0000" (12 ms).
The sine starts and signal is transfered to the output at 33 ms.
Everything is basically working.
Table: uart_mem: rxMem registers V01
Input | memory address | Number of Bits |
rx_data_out | 0 | 8 | received command |
a00000w1w0 | 8 | 8 | a '1' active '0' off
w1w0: 01 sine, 10 triangle, 11 switches |
Step_Re | 16 | 32 | Sine: fine step |
Step_Im | 48 | 32 | Sine: fine step |
Step_Re1 | 80 | 32 | Sine: coarse step |
Step_Im1 | 112 | 32 | Sine: coarse step |
sample | 144 | 24 | Sine: number of samples until repetition |
(offset) | tbd | 32 | Sine: offset voltage |
(amplitude) | tbd | 32 | Sine: amplitude voltage |
tstart | 176 | 16 | triangle minimum start voltage |
tstop | 192 | 16 | triangle maximum stop voltage |
tstep | 208 | 16 | triangle voltage step |
trepeat | 224 | 16 | number of samples per value |
+ EEBench V04
- EEBench V04
EEBench V04
The biggest change for V04 is the use of BlockRAM memory (myBuf) for data acquisition.
After a "U" comman 514 x 5*4 Hex values are sent.
This is shown on the figure below.
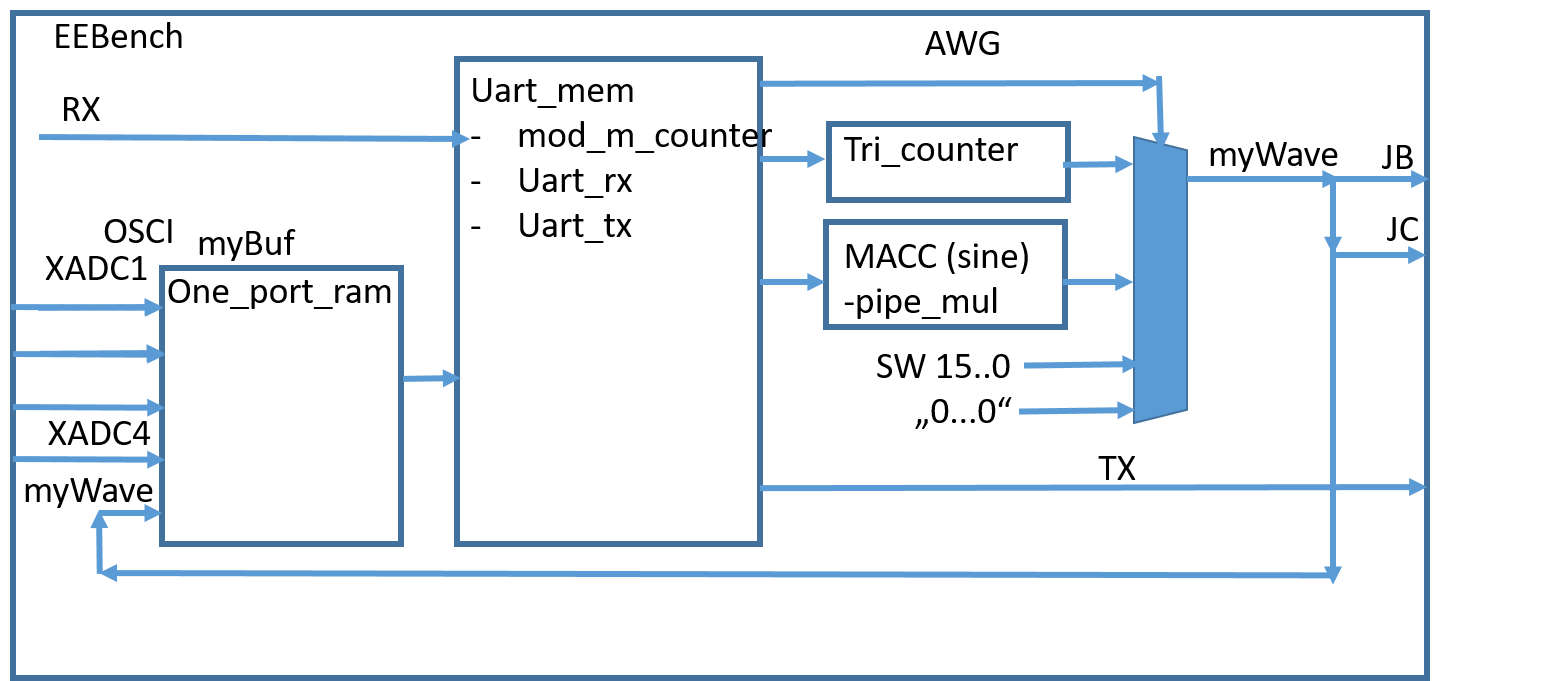
Figure: FPGA blocks for EEBench
Simulation shows:
- Receiving of serial command RX, decoded with SEND trace
- triangle and sine at mywave.
- Data transmission to PC TX and bCount(memory address)
data always zero since no data stored before
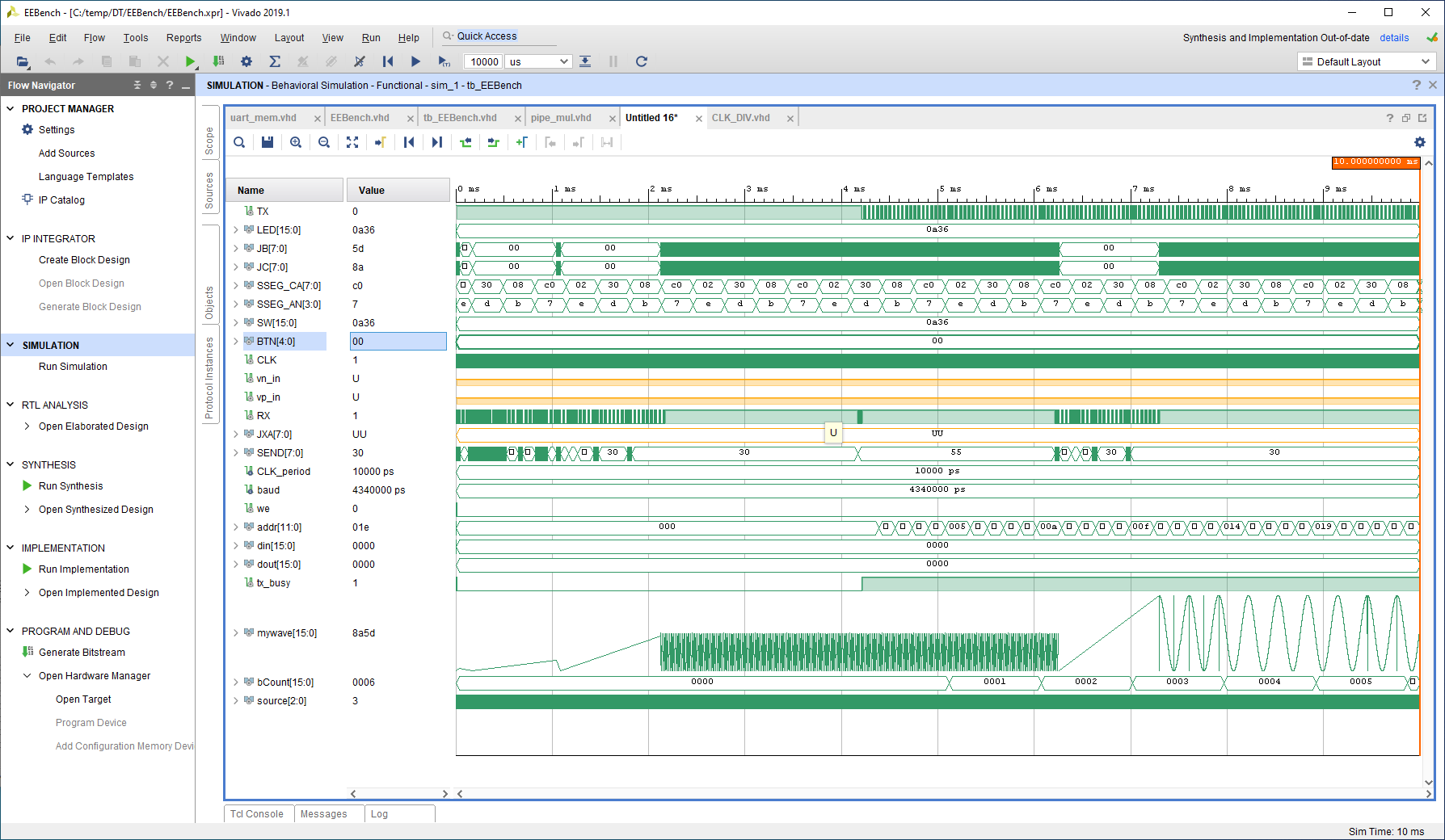
Figure: tb_EEBench.vhdl V04 simulation
Baud rate 230400, 4.34 us per bit, sine command: 25(chars)*10(Bit)*4.3 us(bit time) = 1.1 ms
+ Specification EEBench V05
- Specification EEBench V05
- AWG1:
- 1 channel, 16 Bit R2R output range 0..3.3 V
Sine: 7.69 MHz, tCLK = 130ns synchronized to XADC sampling
Triangle, pulse, stair: fFPGA/repeat maximum 10 ns, 100 MHz
- 2^30 = 2 G points sine:
- DC, pulse, sine, triangle, staircase
- Missing: phase, duty cycle, noise, user defined list, math
- Oscilloscope:
- 4 channel, XADS 1 MBps (multiplexed x8) to 125 kHz, input range 0..1 V
- 256 points buffer: frequency range FFT 450 Hz..50 kHz
- Color coded channels with min, max, average, amplitude, period and frequency
- Missing: Math, processed channel, Cursors, touch operation
- Histogram
EEBench V06
FPGA: Range of oscilloscope time base and buffer size should be extended.
Now the block RAM utilization is 2 out of 50 with 512 points. A factor of 16 8k points should be possible.
The transfer and sample block size should be user controlled.
So a UART command for change of sampling rate (16 Bit) and block size (16Bit) is implemented.
O<sampling><Block size>
Oxxxxxxxx
Update of NEEBench.js
Table: uart_mem: rxMem registers V06
Input | memory address | Number of Bits |
rx_data_out | 0 | 8 | received command |
a00000w1w0 | 8 | 8 | a '1' active '0' off
w1w0: 01 sine, 10 triangle, 11 switches |
Step | 16 | 32 | Sine step |
amplitude | 48 | 32 | Sine amplitude |
offset | 80 | 32 | Sine offset |
(phase) | 112 | 32 | |
(duty) | 144 | 32 | |
tstart | 176 | 16 | triangle minimum start voltage |
tstop | 192 | 16 | triangle maximum stop voltage |
tstep | 208 | 16 | triangle voltage step |
trepeat | 224 | 16 | number of samples per value |
(phase) | 240 | 16 | |
(duty) | 256 | 16 | |
Block size | 272 | 16 | Oscilloscope block size (dataMax) |
Time base | 288 | 16 | Oscilloscope time base (timeBase) |
- EEBench: rMem has already 512 Bits, initialization with 0 implemented
- uart_mem: UART receive set rMem: getCmd: process
when "01001111" => -- ASCII 49 O sine signal
numD := "00001000"; -- 8 Hex numbers, (Step, amplitude, offset)x(8x4)
rmAddress := to_unsigned(276,9); -- Start at index 276 (272 + 4)
rx_mem(7 downto 0) <= rx_data_out;
- Implement signals in EEBench:
dataMax for block size like variable NEEBench and timeBase
hook up rMem to dataMax and timeBase
- For sampling a signal upSample is used
A process sampleRed is created to control sampling
-- sample rate reduction process
--- time Base 000 upSample always 1
-- timebase 001 upSample 1-16-times-0-16-times
-- timebase 010 upSample 1-16-times-0-32-times
sampleRed: process(CLK, BTN(4), readyX)
variable jCnt: integer; -- counter for reduction
variable kCnt: integer; -- 16 samples
begin
if ( BTN(4) = '1') then -- asynchron reset with button 0
jCnt := 0; kCnt := 0;
elsif (rising_edge(CLK) and (readyX = '1')) then
kCnt := kCnt + 1;
if (kCnt >= 8) then -- Clk divider 8 by kCnt
kCnt := 0; jCnt := jCnt + 1;
if (jCnt >= timeBase) then -- upSample short '1' long '0'
upSample <= '1'; jCnt := 0;
else upSample <= '0';
end if;
end if;
end if;
end process;
- TimeBase in NEEBench.html
- Introduce global variable timeBase
- Connect a serial command to change time base
timeBase > 200us/div timeBase = 1
timeBase = timePerDiv / 200E-6
timePerDiv is text input: id="baseVal" with unit value
Update of FPGA with 'Run' command and change in field (functions readCRX,comboBox)
Create function updateOSC for comboBox and readCRX
In updateOSC creat cmdO ="O00200000"; Block size x0020 = 512; timeBase 0 8.32 us
function confOsc() {
var cmdO = "O";
// alert(document.getElementById("dataMax").value);
dataMax = parseInt(document.getElementById("dataMax").value); // 512: 0200
cmdO += decToHex(dataMax,4); // Block size first
timeBase = Math.round(unitToValue(document.getElementById("baseVal").value)/200E-6);
cmdO += decToHex((timeBase + 1),4); // Sampling next FPGA 0 and 1 same!
// update command field
document.getElementById("cmdTxt").value = cmdO;
sendCmdC(); // send OSC configuration
}
window.addEventListener("load",confOsc());
function updateOSC(){
// update value field
updateChanFields();
updatePlot();
confOsc();
}
For debugging send command via tab Configuration cmdTxt.value and sendCmdC()
Attention interaction change during data acquistion? Probably not, only one bad display
Adjusted var timestep in function socket.on('newData', function (data) {
- Verification of timeBase FPGA code and NEEBench.html
Compilation FPGA, html and js correct during loading
Operation: timeBase 0,1 give same maximum sample rate for FPGA -> fix NEEBench
Operation: 2 ms/div x axis not fully filled? Sample rate too high time Base
too low fixed with the following code
timeBase = Math.round(unitToValue(document.getElementById("baseVal").value)/200E-6);
cmdO += decToHex((timeBase + 1),4) // Sampling FPGA 0 and 1 sre the same
- Block size NEEBench: already global variable dataMax present
Tab configuration field 'Sampling memory size' with selection 1,2,4,8,16,512,1024,2048,4096,8182
Read field before sending command
Use field value during receiving data
var timeSampling = unitToValue(document.getElementById("timeSampling").value);
var timestep = timeSampling * (timeBase + 1); // XADC 10ns * 8 * 104 cycles conversion
- Block size FPGA EEBench
- Increase memory size of structure:
one_port_ram.vhdl defines blockRAM
Instance: myBuf: One_port_ram with signal addr (addrUART, addrGen)
uart_mem aBuf, tma, tmAddress
- Increase acquistion
- Increase uart transfer FPGA, ServerEEBench.js, NEEBench.js
- Debugging of block size and sample rate with AWG as reference
and FFT gave 96 dB equivalent to ENOB = 16 Bit
- Open: Challenge of acquisition for large Blocks and large sample times
- At the moment AWG and ADC data is stored all the time in memory.
When a data request is received sampling stops and the data is transfered
as block to the client. This takes 0.5s for 512 data and current baud rate.
The client waits until all block data is received
and updates the chart.
During Run operation every 1 second an Intervall function tries to get new data.
For large blocks or large acquisition times update is very slow.
Solution: There should be a plot every n received data?!
Solution: Large times should have small block sizes and acquisition continues?
- Open:
When to switch from block transfer to individual transfer?
Should the block size be automatically adjusted?
Update setInterval adjustment?
User interface
+ Arbitrary Waveform Generator
- Arbitrary Waveform Generator
For the AWG
(1) A slider for frequency, amplitude and offset with a combobox for value input and selectbox is needed.
(2) The output waveform is displayed in a window.
(3) Run and Stop buttons send commands using a nodejs webserver via the serial interface.
Starting point is a Scientific Project "An open Access FFT-Playground using JavaScript " from
Felix Singer in 2021.
Slider Interface
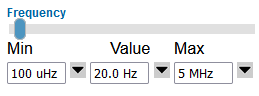
Figure: ComboSlider for the waveform generator
The combo slider is grouped in a table.
Slider:
<input type="range" min="0" max="100" step="2" value="1" class="slider" id="offset1Slider" width="300">
The div for the minimum value has a div with a text field input and an image to activate a select box.
The base name offset1 is extended with Min, Val, Max and the text input CT and select box CB.
<div id="offset1MinCT" style="display:block">
<input type="text" value="1 V" size="5" id="offset1Min" onkeyup="readCR(e,'offset1','V')"/>
<img src="ImagesS/SelectListA.png" width="16" height="16" onclick="comboBox('offset1','Min','CB',1,voltRange,'V')"><br>
</div>
<div id="offset1MinCB" style="display:none">
<select name="offset1MinS" id="offset1MinS" >
<option value="2 V" onclick="comboBox('offset1','Min','CT',1,voltRange,'V')"> 2 V</option>
<option value="1 V" onclick="comboBox('offset1','Min','CT',1,voltRange,'V')"> 1 V</option>
<option value="500 mV" onclick="comboBox('offset1','Min','CT',1,voltRange,'V')"> 500 mV</option>
<option value="-500 mV" onclick="comboBox('offset1','Min','CT',1,voltRange,'V')"> -500 mV</option>
<option value="-1 V" onclick="comboBox('offset1','Min','CT',1,voltRange,'V')"> -1 V</option>
<option value="-2 V" onclick="comboBox('offset1','Min','CT',1,voltRange,'V')"> -2 V</option>
</select>
</div>
Javascript readCR(event, base name, unit):
Reads a key and updates the slider in the range of min and max processing numbers with units.
Updates the text input fields of min, val, max.
In case of the waveform generator the plot is updated.
function readCR(key,id,unit) {
if (!key) { key = event; key.which = key.keyCode; }
if (key.which == 13) { updateSlider(id,unit);}
}
function updateSlider(id,unit) { // From Min Value Max list limit Value
// Min update slider
var minXE = unitToValue(document.getElementById(id+"Min").value);
// alert(minXE);
document.getElementById(id+"Slider").min = minXE
// Max update slider
var maxXE = unitToValue(document.getElementById(id+"Max").value);
if (maxXE < minXE) { // Max greater than Min
maxXE = minXE;
document.getElementById(id+"Max").value = valueToUnit(maxXE) + unit;
}
document.getElementById(id+"Slider").max = maxXE
// Step
document.getElementById(id+"Slider").step = (maxXE - minXE)/50;
// value
var val = unitToValue(document.getElementById(id + "Val").value);
document.getElementById(id + "Slider").value = val;
if (val > maxXE) { val = maxXE; }
if (val < minXE) { val = minXE; }
// position
document.getElementById(id + "Slider").value = val;
document.getElementById(id + "Val").value = valueToUnit(val) + unit;
// update curve
plotAWG();
}
Javascript comboBox(base name,<Min,Val,Max>,slider id, with slider? 1:0, Range,unit):
Updates all fields min, max, val correctly from selectbox.
Javascript to create a section with slider with min, value, max:
function createSlider(id,range,unit) { // Misisng unit V HZ and range name function comboBox readCR
function createComboBox(id,range,unit)
AWG Interface
The basic file is called:
Signalgenerator_22<mm><dd>.html
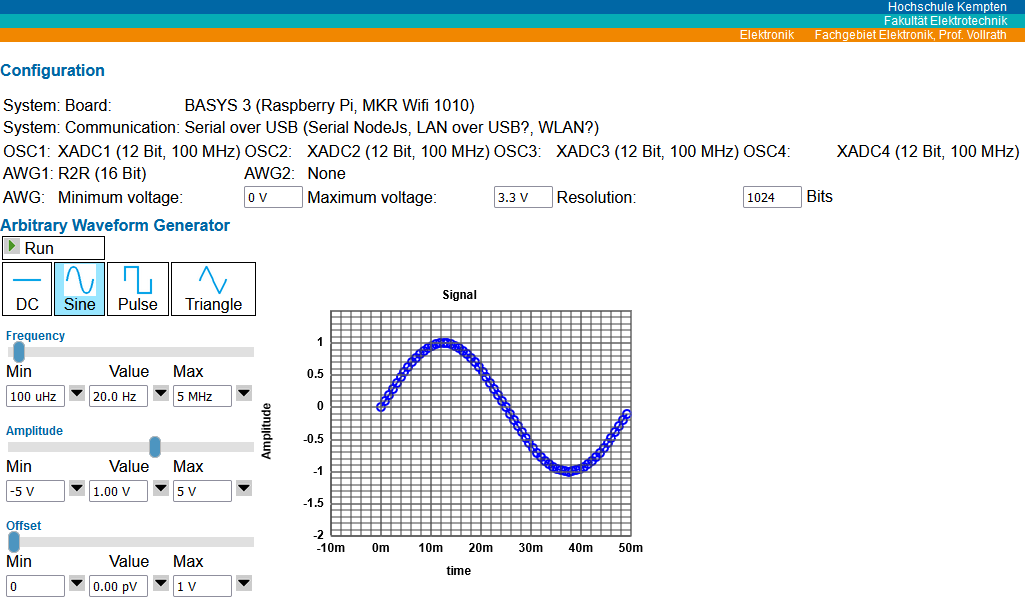
Figure: Signal generator user interface
Used modules are :
<!-- JQuery -->
<SCRIPT SRC="../scripts/jquery.js"> </SCRIPT>
<!-- Chart -->
<script type="text/javascript" src="../Chart_2013_03_11/Chart_basic.js"></script>
<!-- FFT -->
<script type="text/javascript" src="../FFT/dspFFT.js"></script>
For small systems these could be loaded on a user PC via file or via the internet: https://personalpages.hs-kempten.de/~vollratj/
Latest version is: Signalgenerator_221111.html
Challenges were:
Realization of the combined min, max, value, slider with text input and drop down list.
Implementation of units.
Translation of input to uart commands displayed at the bottom
ToDo:
Updating lists with limits
Showing limits offset+amplitude < Vmax and offset-amplitude > Vmin in graph
Connection to nodeJS for run and stop
Choice of voltage, frequency versus code.
Size optimization
+ NodeJS
- NodeJS
Starting point is copying of the HTML and Javascript sources to C:\temp\NodeEEBench
The following files are important:
NodeEEBench.bat this starts ServerEEBench.js
ServerEEBench.js the nodeJS server file
In the subdirectory Projekte the file Signalgenerator_221111.html is located.
An example of nodeJS communication is done
in
Webeditor.
The latest version of serial port on windows requires the following commands:
var SerialPort = require('serialport').SerialPort;
SerialPort.list().then( // List available serial ports
ports => ports.forEach(console.log),
err => console.error(err)
);
var serialPort = new SerialPort({
path: "COM22", // port name
baudRate: 230400 // Baud rate befor 19200, 52 us per bit
});
The io.on subroutine detects user connection and logs it on the console.
Then the socket event of a cmd from the client is implemented.
The most important feature is to detect the block size for sending data.
The serialPort.on 'data' subroutine collects data
from the serial port and emits it to the client.
io.on('connection', function(socket){
var con = true; // connection still valid?
console.log('An user is connected')
// get data from connected device via serial port
var dataBuf="";
socket.on('cmd', function(data){ // get client event
var cmdName = data.value; // cmd passed from client
console.log('cmd: ' + cmdName);
if (cmdName[0] == "X"){
dataBuf = "";
}
if (cmdName[0] == "O"){ // oscilloscope block size next 4 hex values
dataMax = hexToDec(cmdName.substring(1,5));
console.log('Block size: ' + dataMax + "x" + cmdName.substring(1,5) + "x");
}
serialPort.write(cmdName); // hex(cmdName)
// insert server action commands
// var data= "Test Data:" + cmdName;
// socket.emit('newData',{value: data }); // send data to client
});
serialPort.on('data',
function (data) {
// get buffered data and parse it to an utf-8 string
var data1 = data.toString('utf-8');
dataBuf += data1;
// you could for example, send this data now to the the client via socket.io
// io.emit('emit_data', data);
if ((dataBuf.length >= 22 * dataMax ) && (con)) { // complete set
console.log(dataBuf.length/22 + "," + dataBuf.length + "," + dataBuf.substring(0,50)); // dataBuf
socket.emit('newData',{value: dataBuf}); // send data to client
dataBuf = "";
};
} );
socket.on('disconnect', function(data){
console.log('An user is disconnected');
con = false;
});
});
+ Oscilloscope
- Oscilloscope
Oscilloscope FPGA VHDL
Data is sampled (200Hz one period 512 points = 10 us) and stored in block memory (512 x16).
Process sourceSel switches between ADC inputs (1 MSamples per second) serially
since the ADC is multiplexing 4 channels. Also AWG is stored so sampling rate is halved.
Process storeMem transfers values to block memory. Not only ADC values but also AWG values
for reference and debugging are stored
Oscilloscope Acquisition
Client NEEBench.html
A "U" command is serially send to the FPGA.
FPGA:
Sampling is stopped, sampling position is stored at position 2 in block RAM.
Number of samples is stored at position 1 in block RAM to check that really 512 data points
were sampled since last transmit command.
Serial transmission of OSC1..4 and AWG1 in hex format of 512 samples is started.
"U01230123012301230123YX01230123012301230123Y.."
ServerEEBench.js
Receives serial data and transmits each sample of 5 values via an emit to the client.
Client NEEBench.html
Each received data is sorted (lower hex values come first) and decoded (hex to decimal).
After receiving 512 data points (dataOSC), the data is sorted according to the
last sampling position (dataOSC1).
From sample 128 to 384 a trigger position is searched and 256 data points are
selected (variable dataOSC2) and scaled with sample rate and ADC range for display.
dataOSC2 has the final values.
Chart.js is used for display.
Modifications to Chart.js
The color scheme was adapted to nicer colors.
Each curve has to be able to be turned on and off.
Each curve needs a different y-scale. The active
curve y-scaling is displayed in the curve color.
The function ScatterPlotO was created with additional variables: xAxisIndex, activeIndex, channels
The array channels has the properties for each channel.
var objChan = {
name: baseId,
selected: sel,
unit: "V",
offset: 0,
range: 1,
factor: 1,
offScale: 0,
min: 0,
max: 0,
amplitude: 0,
average: 0,
frequency: 0,
period: 0
}
channels.push(objChan);
For each channel the scaling is stored:
for (var kk = 0; kk < channels.length; kk++) {
if (kk != xAxisIndex) {
ymax = - channels[kk].offset + channels[kk].range * 5;
ymin = - channels[kk].offset - channels[kk].range * 5;
Deltay = channels[kk].range; SDeltay = Math.round(channels[kk].range/10);
scaley_fk = canv_obj.height * perSizeY / (ymax - ymin);
scaley_of = yur + ymin * scaley_fk;
channels[kk].factor = scaley_fk;
channels[kk].offScale = scaley_of;
}
}
For plotting each channel is checked for selection and then the scale is set accordingly.
The labeling of the axis is changed using the appropriate color and appropriate scaling.
Oscilloscope User interface
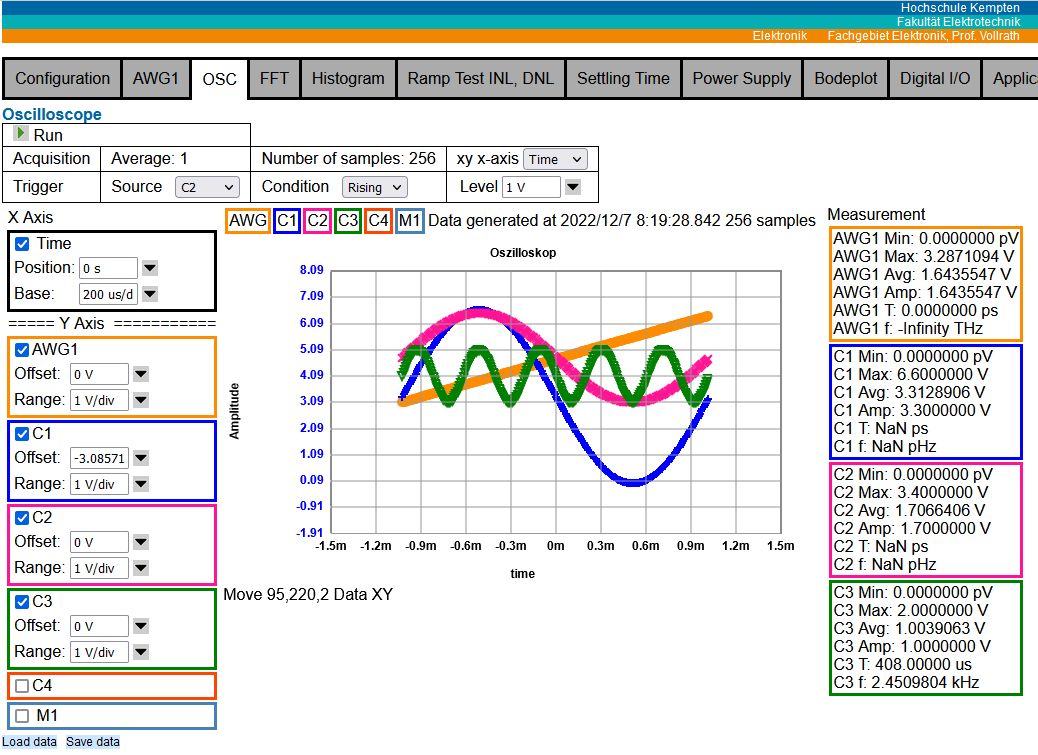
Figure: Oscilloscope interface V05
The figure shows the oscilloscope interface with the run button at the top.
Acquisition options are shown with xy-axis selection operational for version 5.
A trigger source, condition and level can be chosen.
On the left are the axis control with offset (position) and range (base).
Below are 2 buttons to load example data and look at the data with save.
The curves are color coded displayed and typica measurement values are displayed at right column.
Cursors and math functions are still missing.
+ ComboBox
- ComboBox
Since there are a lot of similar elements for one channel
JavaScript is creating all elements.
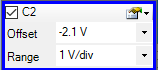
Figure: Example channel configuration interface
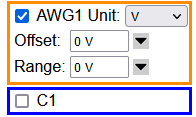
Figure: Realized channel configuration interface
Name, color, Active, Unit list, Offset value, Range value, Offset list, Range list
The lists are depending on the unit and ADC code and input range.
In the list the closest value to the input field is selected.
Run Button
The icon changes from run to stop.
Run emits a serial "U" command from client to server (function oOp('Run'))
and starts a (handlerOsc = setInterval(runOsc,1000);) continues sampling
every second. busyOsc = 1; and oState = "Run"; is set
Stop emits ..(function oOp('Stop')) and sets oState = "Stop";
Acquisition
Version 5:
A block of 512 data points is acquired and searched for a trigger point and
256 data points are selected for display.
5 16 bit values as 4 hex digits each are sent with a start and stop character.
Here is an example for 2 samples 5 channels each.
U4710FF0F471000000000YX0000000000000000D119Y
A new block starts with an "U" and each data value is limited by an X and Y.
Trigger
Trigger implementation
Measurements
Measurement data are generated with function chanStats().
For each channel the data points are searched for minimum and maximum and average is calulated.
var min = dataOSC2[i*dataMax/2];
var max = min;
var avg = min;
for (var i1 = 1; i1 < dataMax/2; i1++) {
var point = dataOSC2[i*dataMax/2 + i1];
if ( point < min) min = point;
if ( point > max) max = point;
avg = avg + point;
}
channels[i].min = min;
channels[i].max = max;
avg = avg/dataMax*2;
channels[i].average = avg;
channels[i].amplitude = (max - min)/2;
Everything is stored in the object array channels.
Average value is used for period and frequency.
Each crossing of the average value of the curve is collected.
// period and frequency
var t = new Array;
for (var i1 = 1; i1 < dataMax/2; i1++) {
var point1 = dataOSC2[i*dataMax/2 + i1];
var point2 = dataOSC2[i*dataMax/2 + i1 - 1];
var point3 = point1;
if (point1 > point2) { point1 = point2; point2 = point3; }
if ((point1 <= avg) && (point2 >= avg)) {
t.push(i1);
}
}
Finally the differnece between 2 crossings and the average of these numbers is used for frequency and period.
// Differences between t(i) half period
var tx = new Array;
for (var i1 = 1; i1 < t.length; i1++) {
tx.push(t[i1]-t[i1-1]);
}
var periodAvg = 0;
for (var i1 = 1; i1 < tx.length; i1++) {
periodAvg += (t[i1]-t[i1-1]);
}
periodAvg = periodAvg / (tx.length-1) * (dataOSC2[1] - dataOSC2[0]) * 2;
channels[i].period = periodAvg;
channels[i].frequency = 1/periodAvg;
The displayed values can be easily selected and copied.
FFT
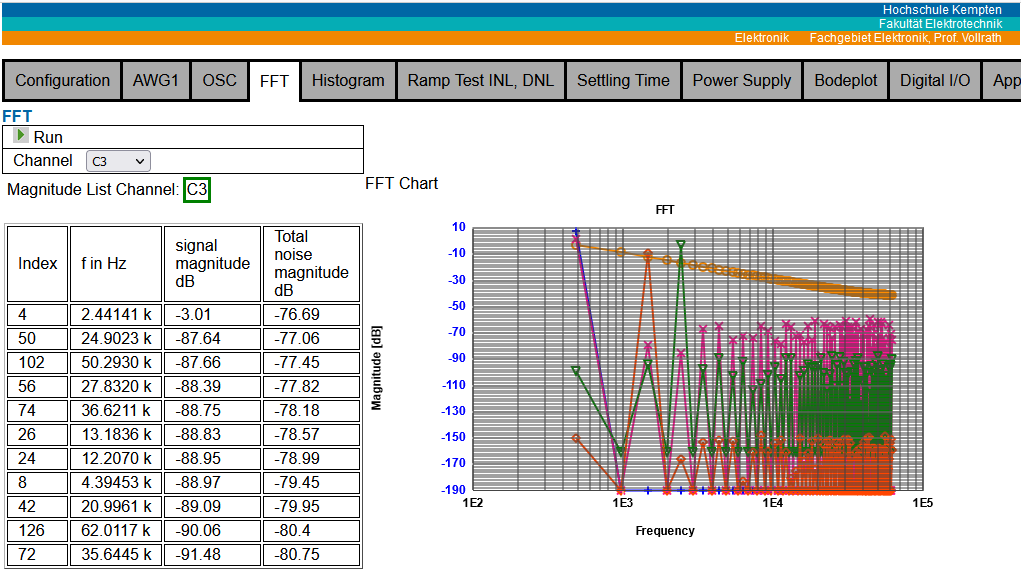
Figure: FFT interface V05
The figure shows the user interface for the FFT. The Run button activates and runs the FFT once.
256 data points at 8.32 us acquisition give a minimum frequency of 4.6 Hz
and a maximum frequency of 60 kHz.
Data was generated internally with the function generateData().
The y values of the channels were scaled by C2 256 (8*6 = 48 dB), C3 4096 (12*6 = 72) and C4 2M (21*6 = 126 dB).
For C3 the largest peaks are listed (choose via channel select list).
For C3 at 2.4 kHz the signal has -3.01 dB and total noise is -76.7 dB as expected.
C1 has 280 dB signal noise ratio equivalent to 280/6 = 46 Bits.
The y axis has a fixed range implemented.
Ideal sine curve calculation can give more than 32 bits -192 dB.
Typical user cases have to be investigated to improve the y-scaling.
Details can be found in FFT Implementation
Histogram
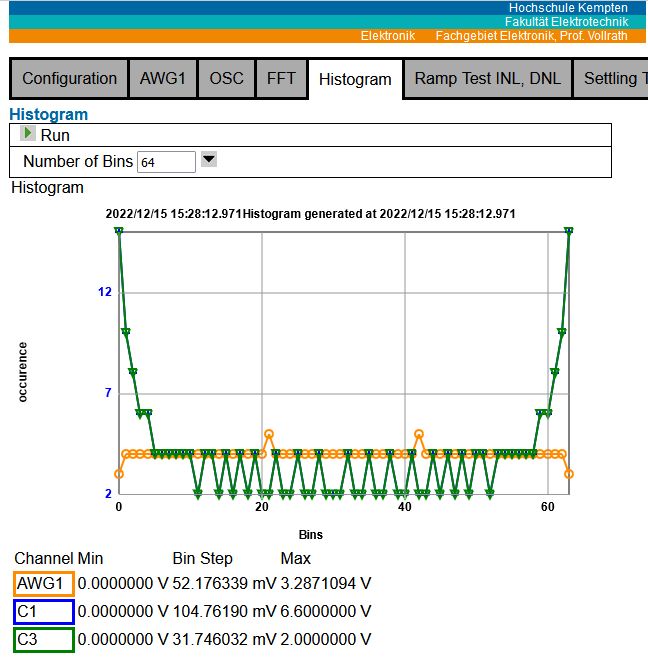
Figure: Histogram interface V06
- Run button (function hOp(cmd))
- Combo box number of bins (var nBin)
- Function generate histogram (var histo = new Array();)
- Chart: canvas id="histoChart"
Settling time (Pulse)
INL, DNL (triangle)
SNR (sine)
Calibration
User circuits
A simple RC circuit.
AWG1 signal is externally applied to an RCL circuit and the output voltage is measured with OSC.
Instead of an RC circuit a switched capacitor Cswitch,CL circuit can be used. The switches should be
digitally controlled. Cswitch should match the R and the output should match the first result.
Cswitch = 1/R/fPGA
Third option would be a digitally processed digital AWG1 signal which is displayed after
signal processing in the OSC window or fed to AWG2 for output and can be measured with OSC.
Voutn+1 = Voutn + (Vinn-Voutn)/R/fCLK/C
Voutn+1 = (Vinn + Voutn * ( R * fCLK *C - 1)) * 1/R/fCLK/C
How does the schematic symbol look like?.
These 3 design options can be compared.
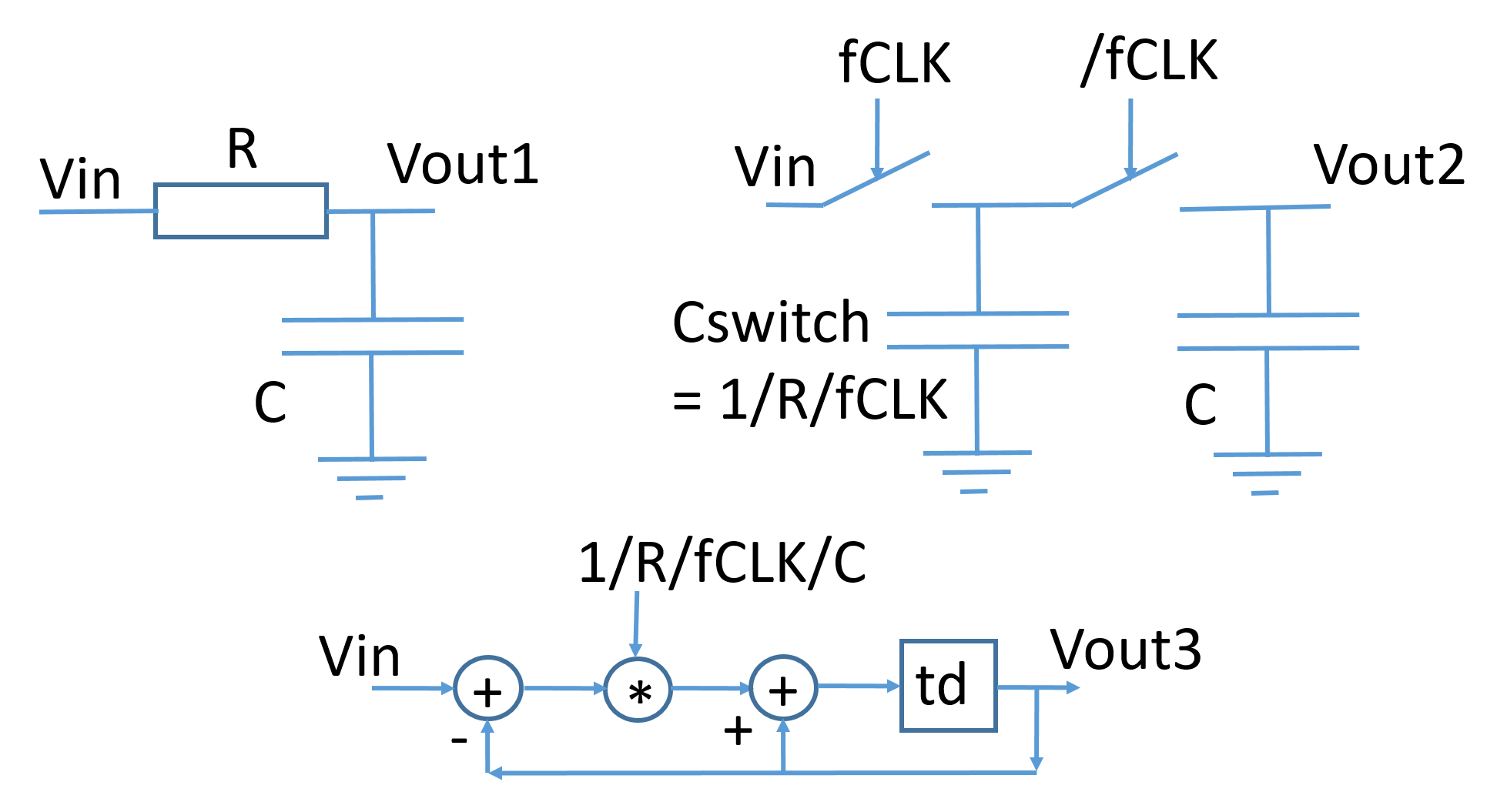
Figure: RC Circuit realizations (td=1/fCLK)
A DAC/ADC error correction
The internal digital sine signal is fed to a lookup table or
equation and then diplayed (OSC) and passed to the external DAC under test.
The OSC input signal is digitally processed via equation or lookup table and
the resulting signal displayed or processed for DNL, INL and SNR.
Filters, control loops, ...
Paralell, seriell conversion
Taking the AWG sine code and converting it to a serial DAC code.
Taking serial gray code output of a pipeline ADC and converting it to binary numbers.
+ More Hardware
- More Hardware
PMODS for BASYS3
ESP32
Arduino MKR Wifi 1010
RaspberryPi
ZYNQ
(12-bit DAC, 1 channel, 1MSs, 8us??, DAC121S101-Q1 (3.-) Digilent PMOD DA2 20.-
16-Bit DAC, SPI, MAX5216 23.-
16-Bit ADC, 12kSps, SPI, MAX11205 18.-
2 channel arbitrary waveform generator and power supplys VPP+, VPP-
AWG1, AWG2, VPP+, VPP-: 12-Bit Quad, 6us, DAC MCP4728 5.-
Mouser 485-4470 Adafruit 4470 MCP4728 Quad I2C DAC 7.50 Digikey 7.30
24-Bit ADC, I2C, 16kSs, 6 channel MAX11259 PMOD 90.- expensive
(12-bit ADC, 4 channel, 1us conversion, AD7991 PMOD AD2
16-Bit ADC 860 SPs ADS1115 6.-
18-Bit ADC 240 SPs MCP3424 5.-
12-Bit ADC 4 channel, ADS1015 12.-
12-Bit DAC 6us I2C MCP4725 7.-
EVAL-AD5443-DBRDZ
(12 Bit DAC I2C 3.4Mbps, 200kHz 1 channel MCP 4725 PMOD
(12-bit ADC 1 MSPS 16 channels, 4 DAC ADuC7020 40.- complex
(12-bit ADC 1 MSs 2 channel AD7476A PMOD AD1 34.-
(8-bit DAC 4 channel PMOD DA1
(12-bit DAC 2 channel, 1MSs, 8us, DAC121S101-Q1 Digilent PMOD DA2 20.-
Waveshare Raspberry Pi AD/DA Expansion Shield Board for Adding High-Precision AD/DA Functions to Raspberry Pi Onboard
ADS1256 (24 Bit 30 KSps 8 chan, DAC8552 (16 Bit, 2 chan, 10us) Sensor Interface
EVAL-ADUC7020MKZ 30.- ARM7 MCU 32-Bit, 12-bit 1 MSps ADC up to 16 channels, 12-bit DAC up to 4 channels
+ Proposal for EEBench hardware
- Proposal for EEBench hardware
A low cost EEBench should be realized.
Components are selected based on the public available resources from (Red Pitaya, Digilent, ADALM)
and prices are looked up at Digikey.
FPGA: ZinQ (XC7Z007S-1CLG400) 61.- (CORA Z7), XC7A35T-1CPG236C 48.71 (BASYS3), XC7S25-1CSGA225C 38.70 CMOD S7
Memory: 512 MBit SRAM (IS61WV204816BLL-10TLI) 25.- (CMOD A7)
Memory: 16 MBit SDRAM 2.65, 8GBit 512Mx16 10..30.-, 1GBit 64Mx16 5.-
ADC: AD9648 Dual 14-bit, 105MS/s, 90.- (Analog Discovery)
DAC: AD5643 15.- Dual 14-Bit Interface: 50 MHz (Analog Discovery) general
DAC: AD9717 30.- 14Bit 125MS/s, AWG
Analog switch: ADG612 6.50 (Analog Discovery)
Amplifier: ADA4940 6.-, AD8066 7.5, ADA4051-2 5.- (Analog Discovery)
Power:
Can a ADC video encoder circuit be used as oscilloscope?
Video CODECS: ADV7281 20.-;
- EEBench Hardware (56+gnd): 32(40) IO, 2 x 16 Bit DAC(AWG) + SPI/I2C Interface, 2 AWG, 2 Vref, VP+, VP-, 3V3VCC, 5VDD 8 Chan OSC
- EEBench Hardware: Breadboard 59x80mm2 29+ pins long: 32 pins gnd,VP+(-),Vref1(2),AWG1(2),gnd,OSC1,2,3,4(5..7),gnd,5(3)V,20 IO,gnd
Breadboard power supply
There should be different versions.
- The simplest solution is just USB connector to breadboard.
- The next would be USB connector and just to generate -Vin
- For battery operation 1..1.5V it would be nice to have 2 * Vin and -Vin
- Voltage control with DAC and PMOD/USB interface would be nice to have for range 2 * Vin and -Vin
- Prefered is a charge pump up to 1.5A
- Prefered is adjustable current limit
Power supply VPP+ VPP- AWG1, AWG2
3V3 VPP+ VPP-
Charge Pump: LM27762EVM 0.25A
OpAmp: 2 x AD8542 (DAC->regulator/AWG)
4 chan DAC I2C: AD5645R (internal reference) 12.-
4 chan DAC I2C 12 Bit MCP4728 Adafruit 4470 8.-
For DAC control I2C interface
SCL Pin 1
SDA Pin 2
ADDR1, ADDR2 jumper GND, VDD, Pin3,4
USB Interface can be realized with ESP32 connected to VCC, GND, SDA, SCL.
Schematic is based on Analog Discovery 2 and LM27762EVM.
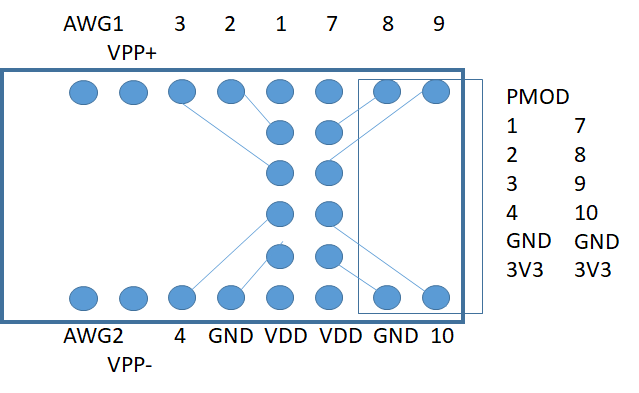
Figure: Board pins for PCB
Missing is the output driver (Opammp, non inverting) for AWG1 and 2 to generate
from 0..3 V 3 to VOUT+ .. VOUT-. (Is this a good concept?)
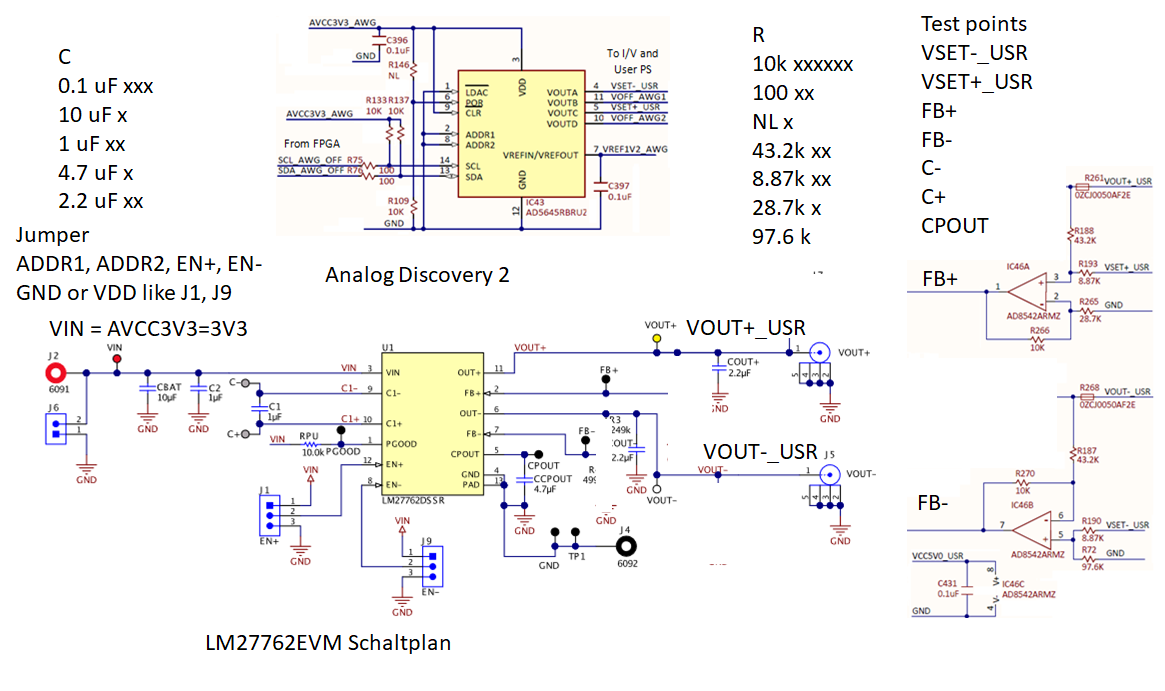
Figure: Power schematic
List of parts:
C: 0.1 uF xxx, 10 uF x, 1 uF xx, 4.7 uF x, 2.2 uF xx
R: 10k xxxxxx, 100 xx, NL x, 43.2k xx, 8.87k xx, 28.7k x, 97.6 k
Jumper: 3 pins/holes for: ADDR1, ADDR2, EN+, EN- (GND or VDD like J1, J9)
PMOD connector female
Breadboard connector 8 pins for top, bottom ( with female connector like Arduino?)
Data Converter GUI
Texas Instruments
Texas Instruments, High Speed Data Converter Pro GUI, User's Guide, SLW087D, march 2017
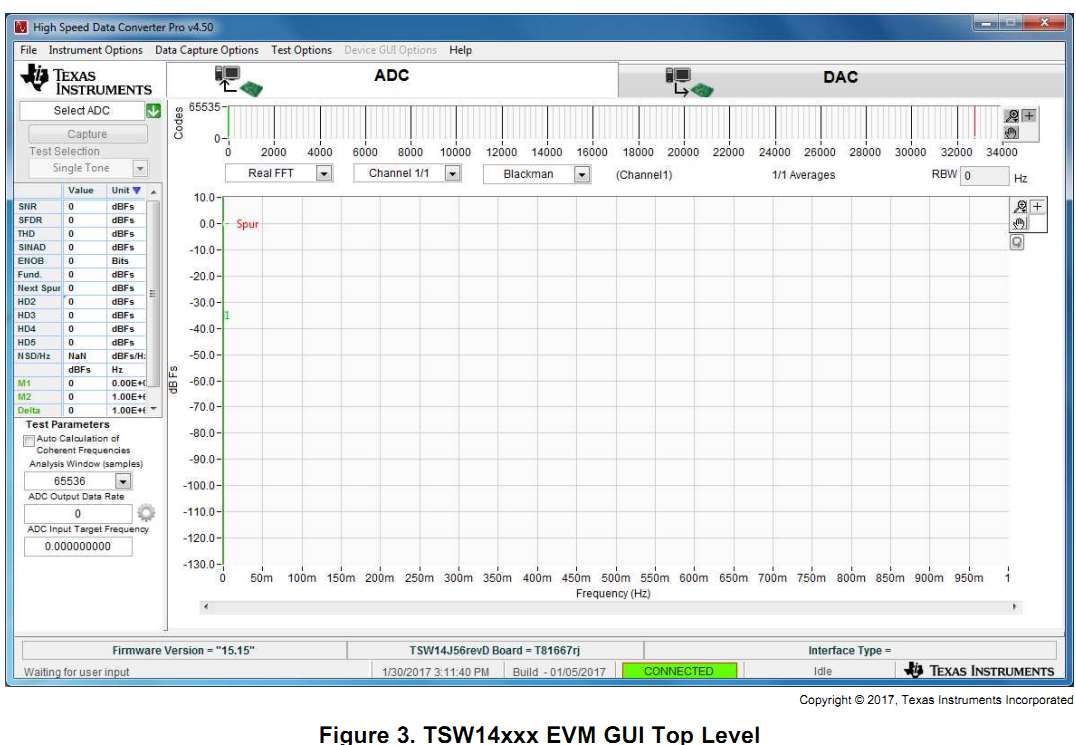
Figure: TI GUI Top level ADC
Select ADC or DAC, Small time window, large FFT window, windowing, code display,
SNR, SFDR, THD, SINAD, ENOB, Fund., Next spurios, HD2, HD3, HD4, HD5
Samples, output data rate, input target frequency
2 channel display
Eye diagram, channel power measurement
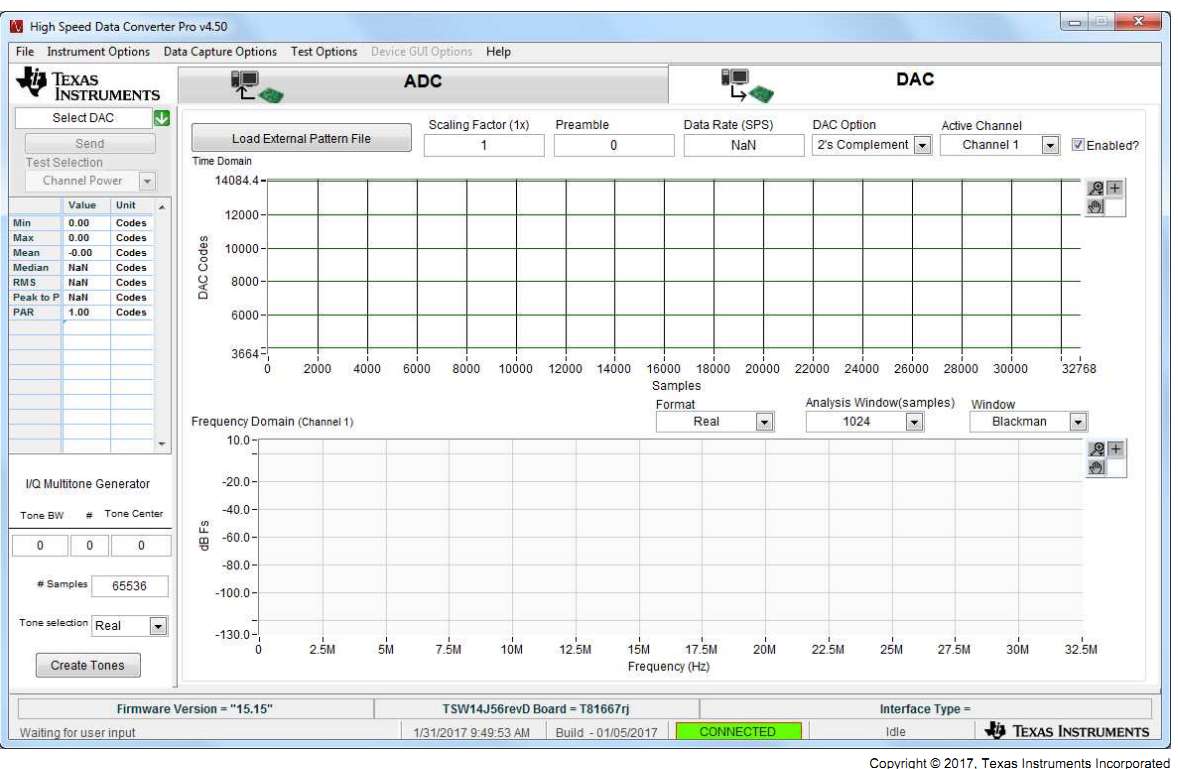
Figure: TI GUI Top level DAC
DAC vector file 16-bit, 16k or 4096..512M vectors
Multitone generator
Example for power: WCDMA_TM1_complexIF30MHz_Fdata122.88MHz_1000.csv
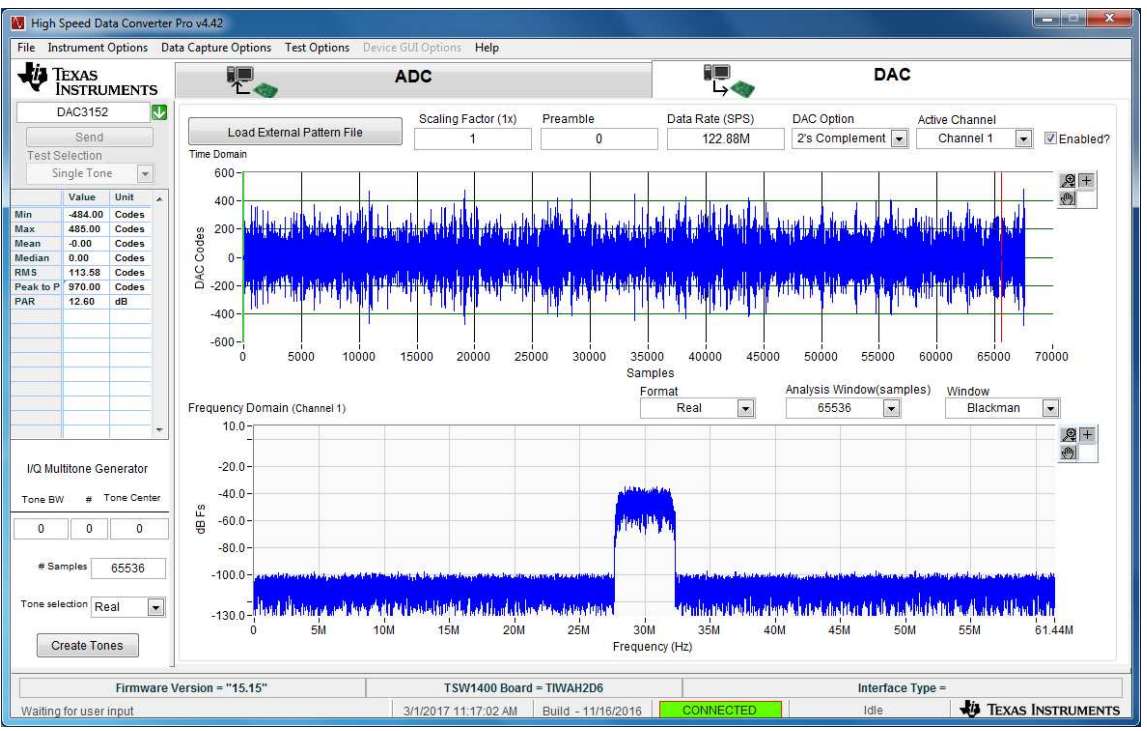
Figure: TI GUI Top level DAC Power
Analog Devices
EVAL-AD7380FMCZ/EVAL-AD7381FMCZ User Guide UG-1304
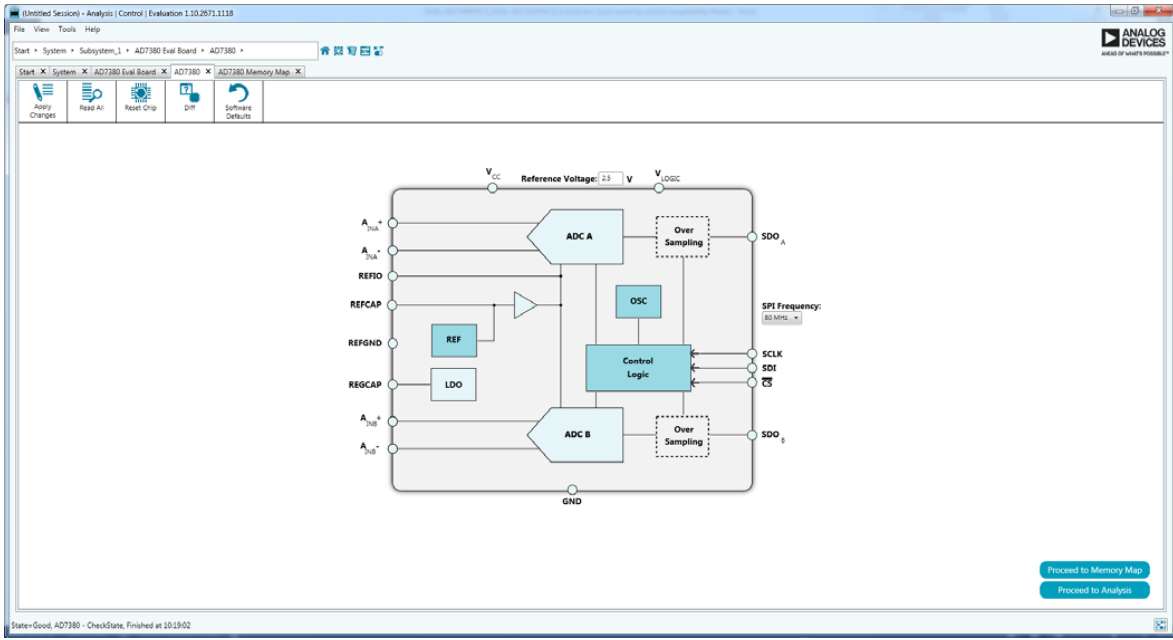
Figure: Analog Devices GUI DAC configuration
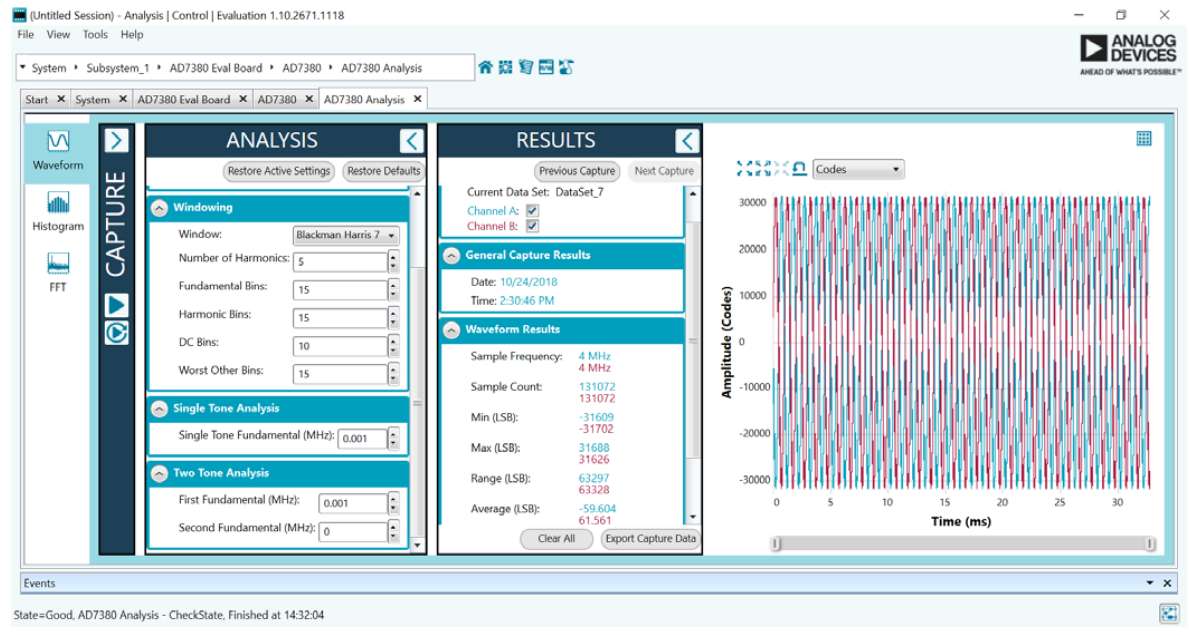
Figure: Analog Devices GUI Waveform
Waveform, histogram, FFT
Maxim, Renesenas
Summary
References
[1] P. Bourke. (1999, Dec.) "Interpolation Methods".
Available: http://local.wasp.uwa.edu.au/~pbourke/
[2] Texas Instruments: ADC Evaluation Platform: PLABS-SAR-EVM-PDK, 499.-
[3] Renesas KMB001 Evaluation ADC System Mouser 351.-
[4] Digilent BASYS3 XADC Demo,
https://digilent.com/reference/programmable-logic/basys-3/demos/xadc
Local References
- Research summary
- EE Bench
- Charge pump
- Video EEbench
- 16 Bit R2R DAC Simulation Characterization
- FFT Implementation
- Trigger Implementation
- NEEBench
|
Dr. Ing. Joerg E. Vollrath received 1989 his
Dipl. Ing. and 1994 his Ph. D. in electrical engineering, semiconductor technology at the
University of Darmstadt, Germany. Since
then he worked for the memory division of
Siemens and Infineon Technologies and
Qimonda in various locations in the USA and
Germany. He is now a Professor for Electronics at the University of Applied Science,
Kempten, Germany. His expertise and interest
lies in the field of design of analog and digital
circuits, programmable logic, test, characterization, yield, manufacturing and reliability.
He has published 30 papers and has currently 32 patents.
|